Ein Gespräch mit Professor Torgersen
Reisswolf: Sie können eindeutig den österreichischen Akzent nicht verleugnen, Ihr Nachname hört sich norwegisch an, in Stanford waren Sie auch. Was haben Sie gemacht nach dem Studium?
Professor Torgersen: Mein Großvater war norwegischer Botschafter in Deutschland und Österreich nach dem Zweiten Weltkrieg. Er hat sich einen Namen gemacht bei der Koordination des Marshallplans. Mein Vater ist in Salzburg geboren, die Familie ist dann aber in Deutschland herumgereist und hatte natürlich immer einen Bezug zu Norwegen. Daher kommt der Name. Und ja, ich habe 28 Jahre in Österreich gelebt, deswegen kriege ich den Akzent nicht mehr weg. Den gibt es in jeder Sprache.
In Stanford habe ich dem Labor von Prof. Fritz Prinz gearbeitet, auch ein Österreicher. Er hat gesagt, er sei stolz auf seine Herkunft und bekommt seinen Akzent auch nicht mehr weg. In der USA stört das auch niemanden, mit einem Akzent weckt man eher das Interesse und kommt ins Gespräch. In Bayern scheint der österreichische Akzent auch kein Problem zu sein.
Nach Stanford bin ich durch Empfehlung von meinem Doktorvater aus Österreich gekommen. Nach Stanford war ich in Norwegen, das war schlicht und einfach das beste Angebot. Ein Einstellungsgrund war auch, dass ich Norwegisch sprach, damit konnte ich Maschinenelemente, einen Grundlagenkurs, übernehmen, der in der Landessprache unterrichtet wird.
Ich habe eigentlich nicht gedacht, dass ich jemals nach Deutschland kommen würde. Ich wurde von einem Headhunter kontaktiert, der mir empfohlen hat, mich auf diese Stelle an der TUM zu bewerben. Die TUM hat mir ein sehr gutes Angebot gestellt, das man nur einmal in seinem Leben bekommt. Ich hätte geplant, irgendwann wieder zurück nach Wien zu gehen, aber ich glaube nicht, dass ich in Wien die Möglichkeiten hätte, die es hier an der TU München gibt.
Reisswolf: Im Vergleich zu Norwegen: Wie gefällt es Ihnen hier, welche Unterschiede fallen Ihnen auf?
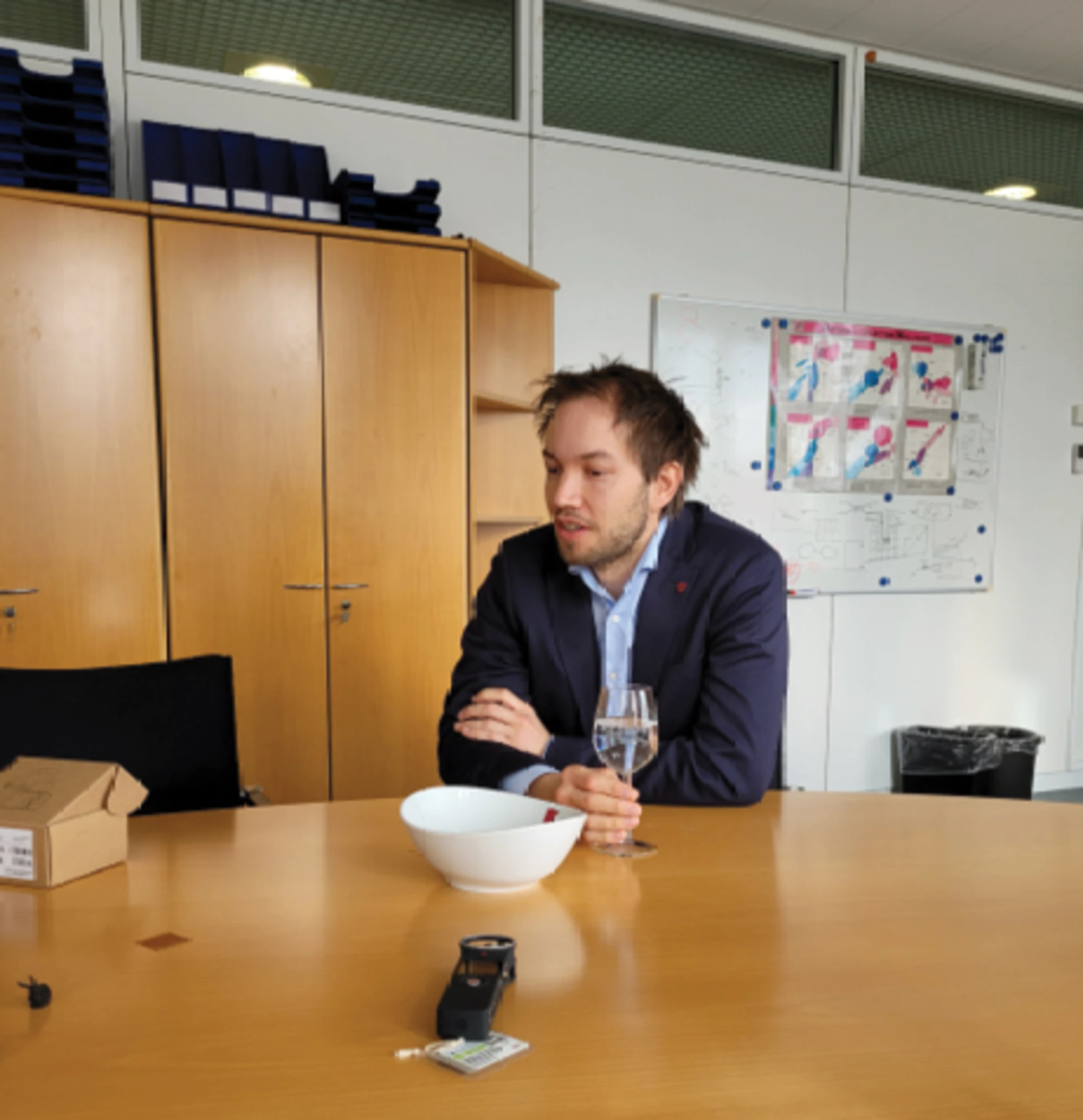
Professor Torgersen: Die Hierarchien sind eindeutig unterschiedlich. Die Lehrstühle sind an der TUM größer und hierarchischer gegliedert, was sicher aus der Tradition gewachsen ist. Der Professor hat die zentrale Rolle und die Lehrstühle sind ihre eigenen Einheiten.
Ich komme von Institutionen, wo es normalerweise ein großes Zentrallabor für gängige Experimente gibt. Alle Forschungsgruppen sind in diesen Zentrallaboren eingemietet, außer sie haben Spezialausrüstung, die sie selbst ständig umbauen. Die Selbstverwaltung der einzelnen Lehrstühle ist mir neu.
In Norwegen sind die Hierarchien sehr flach. Da kommt man schnell zu einer Position, die man vielleicht woanders erst später bekommen würde. Dort konnte ich meine Gruppe aufbauen und hatte auch genug finanzielle Mittel dafür. Das durfte ich schon mit 30, also sehr früh.
Reisswolf: Sie sind Österreicher, ihr Vorgänger Prof. Werner auch, Prof. Mayr ein Stockwerk über uns auch, Herr Krempaszky hier am Lehrstuhl auch. Und in Stanford, Prof. Prinz ebenfalls. Woher kommt es, dass so viele Werkstoffwissenschaftler aus Österreich sind?
Professor Torgersen: Interessant. Gute Frage, weiß ich nicht. In Österreich gibt es die Montanuniversität in Leoben, die ist weltbekannt. Vor allem im metallischen Bereich ist sie sehr stark ist. Mein Doktorvater war als wissenschaftlicher Mitarbeiter in Leoben, obwohl er Physik studiert hat. Auch Prof. Prinz hatte viel mit Leoben zu tun.
Ich habe in Wien die Spezialisierung Werkstoffwissenschaften absolviert. Viele der Lehrenden waren aus Leoben. Mein Vorgänger Prof. Werner hat auch in Leoben studiert. Professor Mayr war in Graz auf der TU, hat aber sehr viel mit der Leobener Montanuniversität zu tun. Ich denke, dass die Montanuniversität Leoben, vor allem im metallischen Bereich, sehr starke Werkstoffwissenschaftler hervorgebracht hat.
Reisswolf: Der Lehrstuhl für Werkstoffwissenschaften hieß früher Lehrstuhl für Werkstoffmechanik und Werkstoffkunde. Wie unterscheiden Sie sich vom Vorgänger, was wollen Sie neu machen?
Professor Torgersen: Der Lehrstuhl hat eine lange Tradition. Er geht auf die Gründungsjahre der TU München zurück, speziell auf Prof. Bauschinger im Jahr 1880. Von ihm gibt es noch ein paar alte Schriften in meinem Schaukasten. Die Mechanik bzw. die Mathematik ist sehr stark im Lehrstuhl verankert, der Fokus war auf Strukturmetallen und deren Mechanik. Mein Vorgänger war ein Experte in diesem Bereich und, wie seine Vorgänger, ein sehr grundlagenforschungsorientierter Wissenschaftler, der herausragende Beiträge geleistet hat.
Meine Forschungsthemen sind eher in Kunststoffen und Keramiken angesiedelt. In meiner Dissertation habe ich mich mit Photopolymeren, also lichtaushärtbaren Kunststoffen beschäftigt. In Stanford habe ich mit Halbleitern zu tun gehabt. In einem Projekt mit BASF und Samsung haben wir Dynamic Random-Access Memory-Strukturen gebaut. An Materialien zur Energiespeicherung und -konvertierung hat meine Gruppe und ich dann auch in Norwegen gearbeitet, und diese Forschung habe ich hierher mitgenommen.
Ich habe ein großes EU-Projekt aus Norwegen mit an die TUM genommen. Es ist ein ERC-Grant, gefördert durch den europäischen Forschungsrat. Diese Projekte sind grundlagenorientiert, es gibt keine Firmenbeteiligung. In unserem Projekt geht es um die Materialentwicklung für Brennstoffzellen.
Mit den Werkstoffwissenschaften als Überbegriff will ich die Tradition des Lehrstuhls als grundlagenorientiertes Institut weiterführen, jedoch auch andere Werkstoffe wie Nichtmetalle und speziell die Energiematerialien unterbringen.
Reisswolf: Was sind Energiematerialien?
Professor Torgersen: Das sind Materialien, die dazu verwendet werden, Energie zu speichern, oder sie umzuwandeln. Wir fokussieren uns im Moment auf die Elektrodenproduktion für die Brennstoffzelle und für Elektrolyseure. Diese Elektroden beinhalten eine Vielzahl an Materialien, die verbaut werden müssen. Wir versuchen im Moment Karbon-, oder Kohlenstoffelektroden aus dem 3D Drucker herzustellen. Karbon wird in Zukunft ein interessantes Material sein, weil es davon genug gibt. Es ist leitfähig, leicht und steif. Karbon ist zwar sehr spröde, aber es eignet sich gut als Basismaterial für Elektroden von Batterien und Brennstoffzellen. Stahl wird heute als Elektrode noch verwendet, hat aber bei der Hochskalierung Probleme, da er sehr viel schwerer ist.
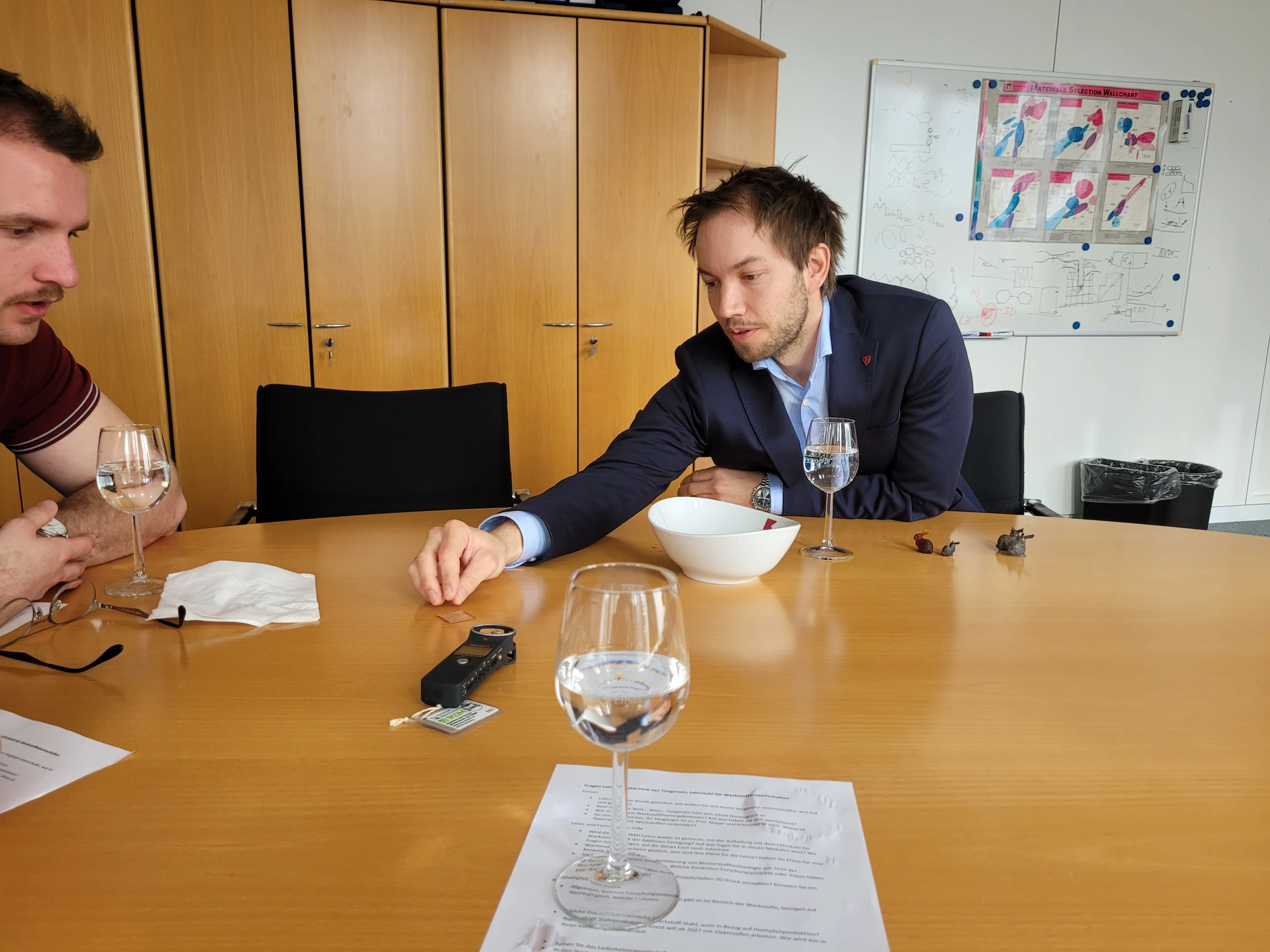
Für die Herstellung von 3D gedrucktem Karbon, haben wir einen Prozess entwickelt. Karbon stellt man normalerweise durch Karbonisieren (Temperaturbehandlung in Schutzgasatmosphäre) als Faser her. Durch die Anordnung der Fasern, kann man dann ein 3D Bauteil herstellen. Die Fasern bleiben jedoch heterogen. Wenn man aus Fasern Elektroden baut, hat man sehr wenig Kontrolle über die Geometrie und damit auch die Transporteigenschaften zum Transport von Reaktionspartnern und -produkten in einer Batterie oder Brennstoffzelle. [Zeigt auf Elektrode, siehe Bild oben] Das ist eine Elektrode einer Brennstoffzelle, die ist ungefähr so dick, die Kanäle von dieser Elektrode sind im mm Bereich, die kann man sehen. Jedoch die darunterliegenden porösen Schichten sieht man nicht, weil die so dünn sind. In einer Brennstoffzelle muss man viel unterbringen: Kanäle, Poren, katalytische Schichten und vieles mehr. Unsere konventionellen Herstellungsmethoden erlauben uns nur einen schichtweisen und sehr heterogen Aufbau, der aber viel Optimierungspotential hat, um den elektrischen Effekt zu maximieren. Wir versuchen, Elektroden am Computer zu modellieren und dann mit einem hochauflösenden 3D-Druck dimensionsgetreu nachzubauen. Das Neue an diesem Prozess ist, dass wir die Möglichkeit haben, die Geometrie des Bauteils aus dem 3D Druckprozess im Karbonisierungsprozess zu erhalten, die Polymerstrukturen aus dem 3D Drucker schrumpfen zwar, bleiben aber in ihren Dimensionen stabil. Den Schrumpf kann man vorhersagen, und vorher bei der CAD Geometrie berücksichtigen.
Das ist beispielsweise so eine dimensionsstabile Karbonstruktur. [Prof. Torgersen zeigt auf einen Carbon-Hasen, siehe Bild rechts] Die schaut vielleicht filigran aus, aber die können Sie sicher nicht zerstören, auch wenn Sie sie gegen die Wand schmeißen. Das Ausgangsprodukt, der viel größere, nicht-karbonisierte Hase, ist bei einer Firmenveranstaltung kaputt gegangen, weil er sehr spröde ist. Das Ausgangsmaterial karbonisieren wir, es schrumpft in allen Richtungen zusammen und wird ein ganzes Karbonteil. Karbon kann man sehr schwer fräsen, deswegen sind solche Bauteile mit diesen Dimensionen in Karbon gar nicht anders möglich als mit unserem Prozess. Schwierig wird es, wenn das Bauteil großvolumig ist. Wenn das Bauteil in alle Richtungen schrumpft, müssen aus der Mitte des Bauteils nichtkarbonisierbare Stoffe (CO2, Wasser und kürzere Hydrokarbone) rausdiffundieren. Die Transportwege werden umso länger, je dicker das Bauteil (hier: der Hase) ist. Die Hasen hier sind relativ einfach zu karbonisieren, weil sie aus dünnen Stäben bestehen, es ist also nicht viel Distanz zur Umgebung ist.
Reisswolf: Der Trend entfernt sich von Massivstrukturen, hin zu hohlen Strukturen. Zum Beispiel wurden Triebwerkschaufeln früher aus dem Vollen gefräst. Jetzt gibt es zumindest Versuche, dass man die mit einer gewissen Hohlstruktur baut. Haben voluminöse Strukturen noch Relevanz?
Professor Torgersen: Da ist natürlich die Frage, was man erreichen möchte. Für Brennstoffzellen selbst sicher nicht, da sollte man eher schauen, dass sie so dünn wie möglich bleiben. Je dünner sie sind, desto weniger ohmsche Verluste hat man. Aber man braucht auch den notwendigen Platz, um die Massentransporte steuern zu können. Es ist also nicht die Frage nach dem Volumen sondern die Frage nach der Breite an Dimensionen, die man mit einem Prozess abdecken kann. Wenn man den Hasen als Beispiel nimmt: Das Ohr hat viel mehr Oberfläche als der Körper. Die Fähigkeit, alles auf einmal zu karbonisieren erlaubt eine breite Spanne an Dimensionen zu reproduzieren. Für die Brennstoffzelle bedeutet das, dass man viele der Schichten, die mit unterschiedlichen Herstellungsverfahren produziert wurden, in einem Verfahren herstellen kann. Damit kann man Lagen konsolidieren und die Bauteile (Elektroden) effizienter machen.
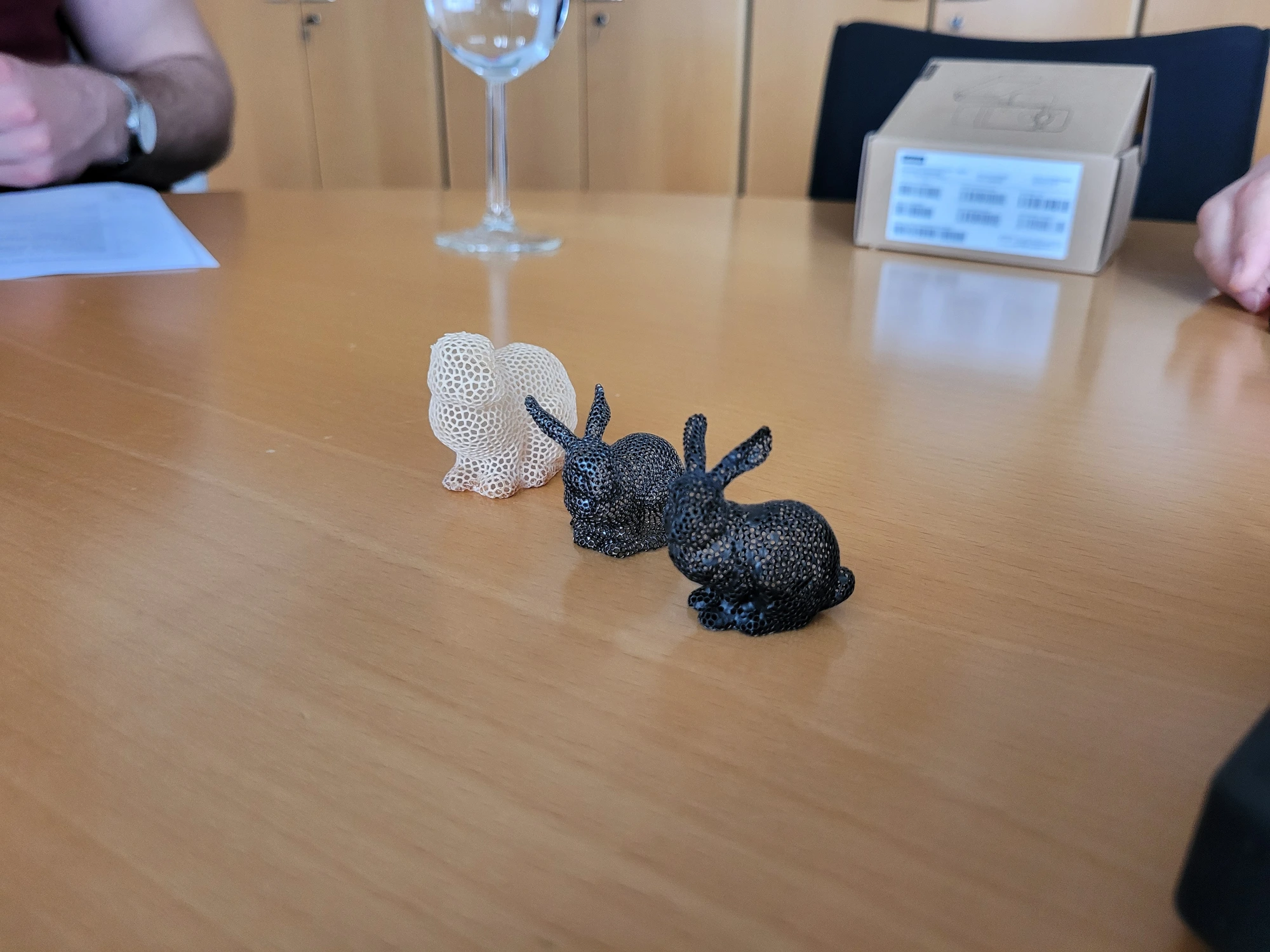
Ganz generell sind großvolumige Strukturen sehr wichtig, nicht nur in der Konstruktion. Um beim Thema zu bleiben; wenn man elektrischen Strom transportieren möchte braucht man große Querschnitte um die Verluste gering zu halten.
Reisswolf: Wie funktioniert das Karbonisieren?
Professor Torgersen: Man druckt mit einem 3D-Drucker diese Strukturen aus einem Polymer, bei dem wir nicht sagen dürfen, was es ist. Die fertige Struktur stellt man in einen Ofen und spült diesen mit Stickstoff. Dann fährt man einen mehrstufigen Temperaturzyklus, sodass das Bauteil isotrop in alle Richtungen gleich schrumpft. Der Temperaturzyklus ist komplex, mit dem haben wir uns lange beschäftigt. Aber im Endeffekt geht es nur um Haltezeiten, Rampen, Abkühlen und Aufheizen.
Eine Brennstoffzelle oder eine Batterie besteht nicht nur aus Karbon, sondern auch aus vielen anderen Materialien. Und da kommt das ins Spiel, was Sie gesagt haben, wenig Material brauchen. Wir beschäftigen uns mit dem Prozess der Atomlagenabscheidung, einen Prozess, den ich aus Stanford mitgebracht habe. Atomlagenabscheidung ist ein Beschichtungsprozess, in dem eine Atomlage pro Zyklus wächst und dann von selbst stoppt. In einem zweiten Prozess wird die Atomlage wieder oxidiert und man kann die nächste Atomlage aufbauen. Mit dem Prozess haben wir Platin auf Elektroden für Brennstoffzellen abgeschieden und so die Massenaktivität erhöht. Massenaktivität heißt, wie viel Platin braucht man, um Sauerstoff zu spalten. Es geht darum, wie viel Platin man an die Oberfläche packen kann. Je mehr Platin an der Oberfläche, umso höher ist die katalytische Aktivität für die Sauerstoffspaltung und desto weniger teuren und seltenen Werkstoff (Platin) braucht man. Die Atomlagenabscheidungsprozess eignet sich hier besonders.
Für Iridium gibt es eine gute Analogie. Die Elektrolyse in Deutschland soll hochskaliert werden, und das mit einer sehr zukunftsreichen Technologie, der PEM-Wasserelektrolyse. Polymer Electrolyte Membrane bezieht sich auf den Separator, eine Polymerschicht, durch die Wasserstoffprotonen durchdiffundieren können. Wenn die Aufskalierung der Wasserstoffproduktion mit PEM-Wasserelektrolyse funktionieren soll, brauchen wir schon jetzt das gesamte Iridium, das auf der gesamten Welt abgebaut wird, um mit der Produktion nachzukommen. Es gibt wenig Alternativen zu Iridium, bzw. sind haben alle Alternativen massive Nachteile. Wenn wir das durch Iridium mögliche Leistungsniveau erhalten wollen, ist es unumgänglich, dass der Materialeinsatz reduziert wird. Damit beschäftigen wir uns auch: Wie kann man seltene Erden nicht ersetzen, sondern einfach in einem geringen Maße verwenden, ohne Leistungseinbuße zu haben.
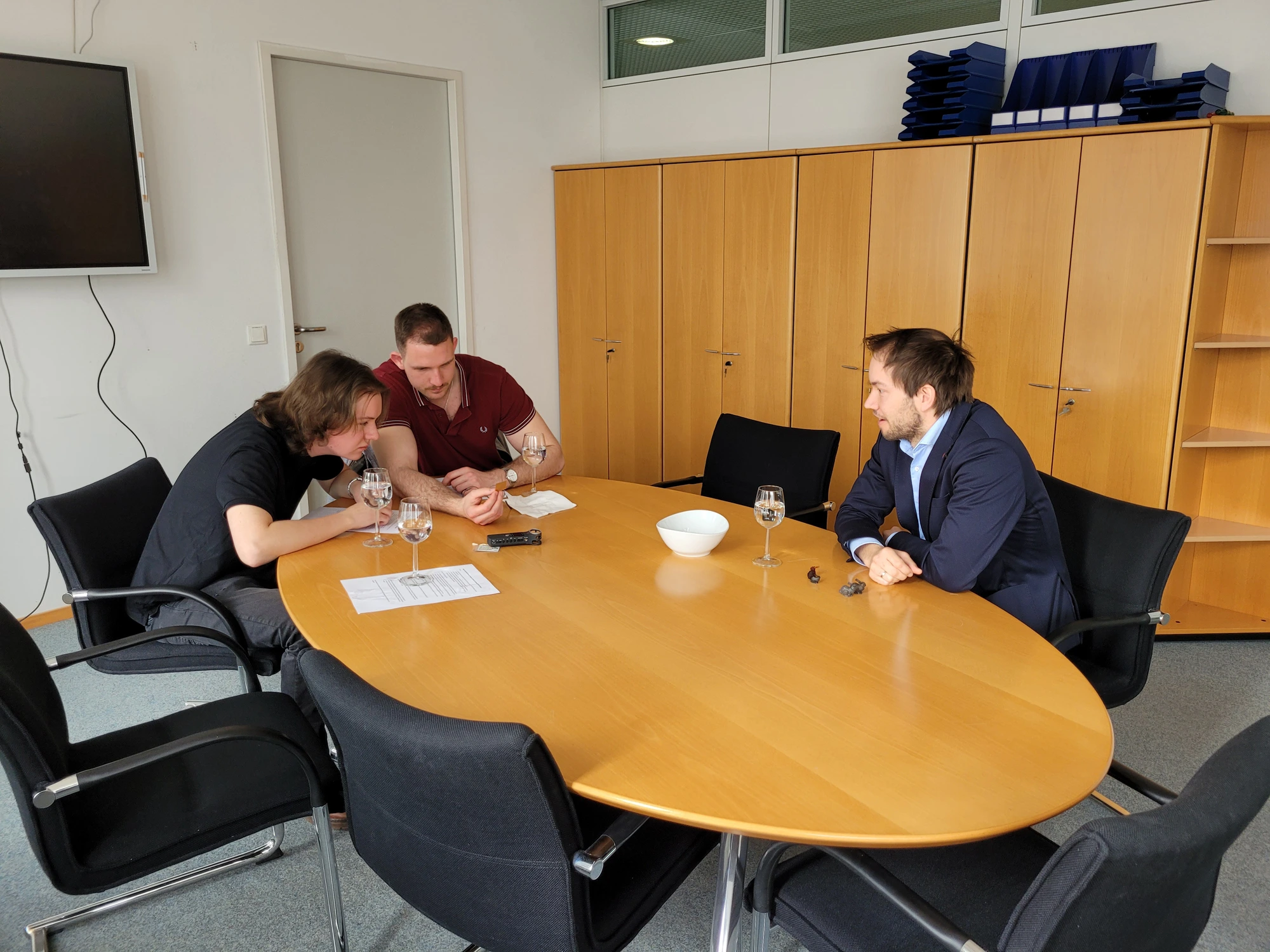
Reisswolf: Welche Zukunft hat der klassische Werkstoff Stahl? Auch wenn Sie sagen, dass Sie vor allem mit Karbon und anderen Materialien arbeiten. Würden Sie sagen, dass Stahl oder auch die Hochofenproduktion Zukunft haben?
Professor Torgersen: Grundsätzlich ja, weil Stahl unser wichtigster Strukturwerkstoff ist. Wir müssen nur auf zwei Dinge aufpassen. Erstens, Stahl muss aus CO2-neutralen Prozessen produziert werden. Da gibt es viele spannende Entwicklungen. Zum Beispiel kann Stahl mit Wasserstoff gewonnen werden. Ohne Experte auf dem Thema zu sein, glaube ich dass dann mehr Schrott notwendig ist, um einen ähnlichen Kohlenstoffanteil wie bei herkömmlichen Hochofenprozessen zu erhalten. Solche Prozesse sind essenziell, um klimaneutral zu werden.
Der andere Aspekt ist der sehr hohe Mix an Materialien. Je komplexer das Material aufgebaut ist, desto höher ist seine Leistungsfähigkeit. Ein klassischer Fall ist zum Beispiel karbonfaserverstärkte Kunststoffe. Solche komplexen Werkstoffe sind teilweise maschinell nicht herzustellen, haben aber eine hohe Steifigkeit und ein geringes Gewicht. Die erhöhten Kosten rechnen sich für Hochleistungsanwendungen, wie beispielsweise die Luftfahrts. Das Recycling eines solchen Werkstoffes ist jedoch sehr schwierig.
Bei Halbleiter gilt das Gleiche: je dünner die Schichten, je mehr Grenzflächen, je höher der Materialmix, desto höher die Leistungsfähigkeit, und desto schwerer wird es zu rezyklieren.
Das gilt auch beim Stahl. Wir bewegen uns immer weiter in Richtung Elektromobilität. Das bedeutet, dass viel Kupfer verbaut wird. Wenn man das Auto verschrotten muss und zusammenpresst, ist der Kupfer mit dem Stahl vermischt. Der Kupfer versprödet den Stahl jedoch extrem. Schon bei 4 bis 5% ist der Stahl nicht mehr brauchbar. Es ist dann sehr viel Frischeisen notwendig, um den Kupferanteil wieder unter in tolerierbares Niveau zu bringen.
Stahl wird immer eine Rolle spielen, und das Wissen über Stahl ist essentiell, aber wir müssen den ökologischen Fußabdruck bei der Produktion und beim rezyklieren von Stahl beachten. Wen wir so weitermachen wie bisher, kann es sein, dass wir irgendwann keinen Stahl mehr haben. Mir fallen auf Anhieb zwei bis drei Artikel ein, die prognostizieren, dass ab 2050 kein Stahl mehr zur Verfügung stehen wird, weil der Kupferanteil zu hoch wird. Und da geht es nur um Kupfer, andere Elemente haben ähnliche Effekte auf Stahl.
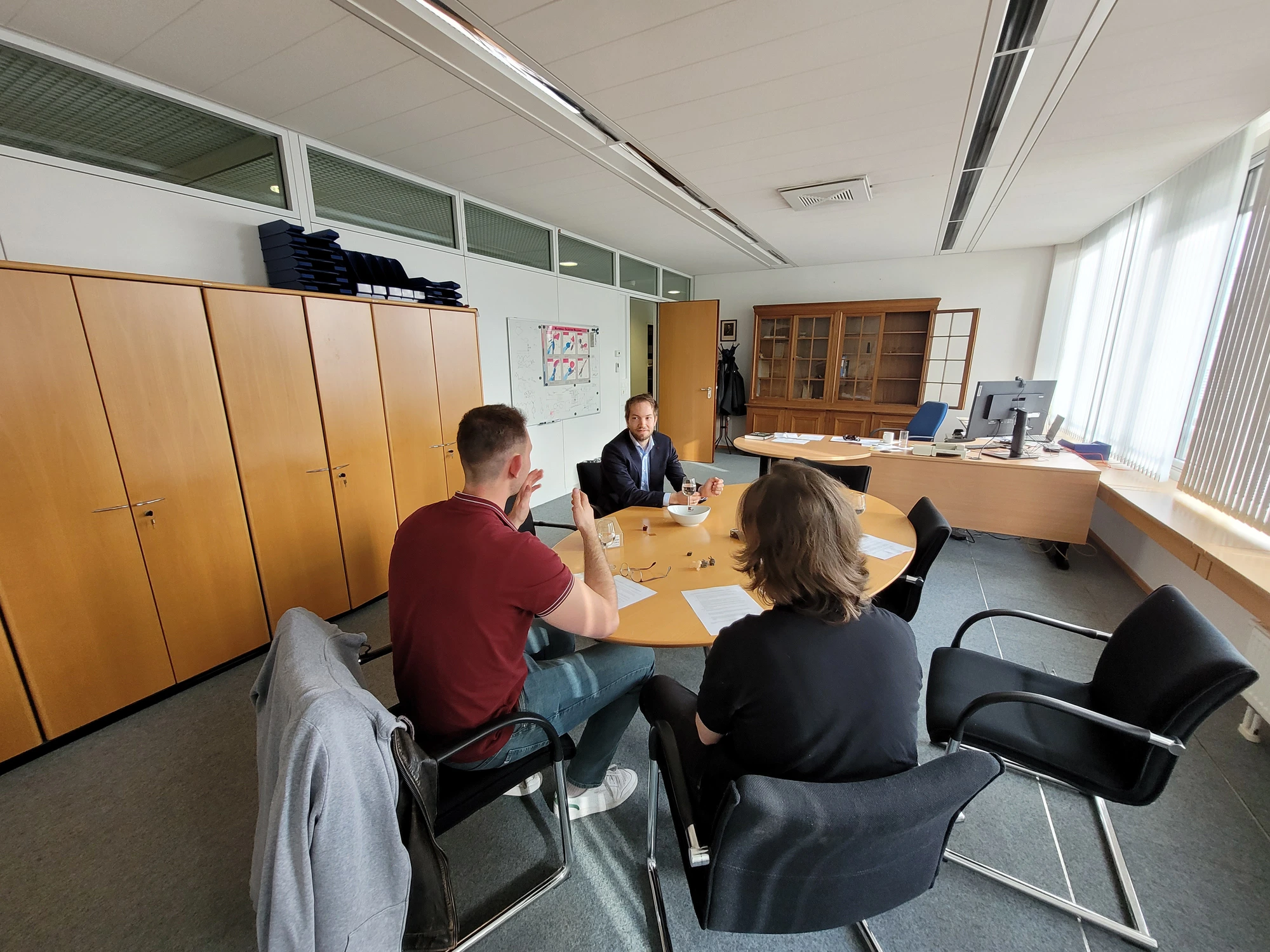
Reisswolf: In der Lehre teilen Sie sich die Fächer Werkstoffkunde 1 und 2 mit dem Lehrstuhl für Werkstofftechnik der Additiven Fertigung. Wird das so weitergemacht? Worauf legen Sie in diesen Modulen Wert?
Professor Torgersen: Wir wollten so weitermachen, wie gehabt, da jeder Lehrstuhl seine Spezialthemen hat. Dieses Spezialwissen können wir in diesem Konzept besser vermitteln. Letztes Semester war es noch nicht optimal, wir hatten einige Anfangsschwierigkeitn. Da wird sich sicher noch einiges verbessern.
Wir werden den Fokus etwas weg von den metallischen Werkstoffen setzen. Die metallischen Werkstoffe sind zwar sehr wichtig, aber es gibt auch andere Werkstoffe, die immer wichtiger werden. Im WK2-Plan ist das bereits berücksichtigt. Die Strukturwerkstoffe werden am Anfang behandelt, dann fokussieren wir uns aber auch auf verschiedene Keramiken und Polymere. Auch die Halbleiter werden wir beleuchten, damit unsere Studenten zumindest einmal ein Banddiagramm gesehen haben, was für Energiematerialien sehr wichtig ist. Dann werde ich auch über Batteriematerialien und Katalysatoren reden, da die Elektrochemie in Zukunft immer wichtiger wird und auch vor dem Maschinenbau nicht mehr haltmacht. Es gehen auch immer mehr Jobs die diese Kompetenz erfordern. Reine Strukturwerkstoffe, die nur schlicht und allein Strukturaspekte erfüllen, wird es immer weniger geben. Tesla baut Batterien als Strukturwerkstoffe. Durch die immer komplexer werdenden Werkstoffe, sind auch Aspekte von Recycling in die Werkstoffkunde einzubringen. Das ist unsere gesellschaftliche Verpflichtung.
Reisswolf: Haben Sie auch ein Wahlmodul für den Bachelor geplant? Was sind Ihre Pläne für die Lehre?
Professor Torgersen: Ein Praktikum wollen wir längerfristig wieder anbieten, wo man dann, wie früher, selbst Zugprüfungen durchführen kann. Wir haben geplant, diese Praktikum mit Polymeranalytik (TGA, DMA, DSC,…) zu kombinieren. Die Rastelektronenmikroskopie soll auch eine Rolle spielen. Das Praktkum haben wir noch nicht ausgearbeitet.
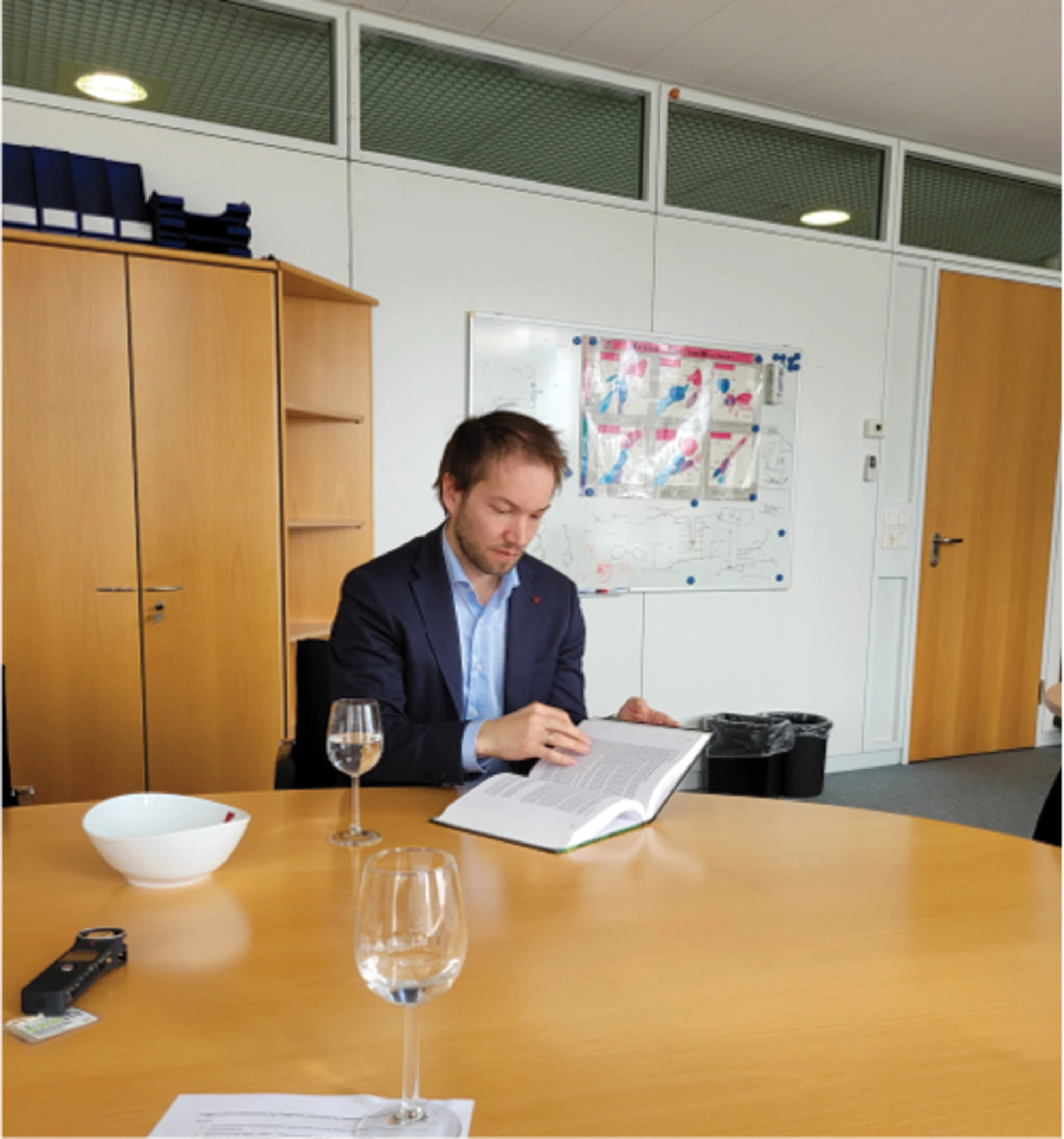
Für die Spezialisierung haben wir uns überlegt, einen simulativen Kurs im Bereich der Molekulardynamik anzubieten. Molekulardynamik ist eine Anwendung von Newtonscher Mechanik auf Molekülketten. Mit dem Prinzip kann man viele dynamische Prozesse in einem Werkstoff simulieren, zum Beispiel Rissinitiierung, Versetzungsbewegungen oder auch chemische Reaktionen, thermisches Verhalten.
Reisswolf: Teil Ihrer Forschung ist das INCITE-Projekt. Das wirkt gar nicht wie die klassische Werkstoffkunde. Worum geht es da?
Professor Torgersen: Beim INCITE-Projekt geht es um Krebsforschung, bzw. geht es um die Selektion von T-Zellen, effektive Zellen, die den Krebs bekämpfen können. Da bin ich von den Biologen in Trondheim angesprochen worden, ob ich mitmache.
Grundsätzlich geht es darum, dass man einen Mikrochip baut, den man mit einem Zellmedium durchspült, sodass sich drei Arten von Zellen ablagern. Es gibt Endothelzellen, auf denen sich dendritische Zellen ablagern. Die dendritischen Zellen geben den Anreiz, T-Zellen zu binden. Mit den dendritischen Zellen kann man die Selektion dieser T-Zellen steuern. Wenn die sich anhaften, gibt es einen bestimmten Mechanismus, den man nachbilden und modellieren kann. Und der sagt etwas aus über die Effektivität dieser T-Zelle, sich an bestimmte Krebszellen zu binden und diese auszulöschen.
Es ist also ein Immunotherapie-Projekt, ein absolutes Grundlagenforschungsprojekt, mit vielen verschiedene Institutionen zusammen unter dem FET-Open Schirm. Was das wieder mit Werkstoffwissenschaften zu tun, ist auch eine gute Frage. Dieser Scaffold oder dieser Microchip muss bestimmte Voraussetzungen erfüllen. Er soll erst einmal biokompatibel sein, und er darf sich nicht abbauen. Biokompatibilität und Bioabbaubarkeit sind unterschiedliche Dinge. Außerdem muss sich das Konstrukt mit Endothelzellen besiedeln und durchspülen lassen können, damit sich die dendritischen Zellen zwar schnell durchbewegen, aber trotzdem anhaften. Man muss die Zellen einer gewissen Scherrate aussetzen, damit sie sich überhaupt mit den Zellen verbinden. Nach dem Anhaften der dendritischen Zellen, muss noch immer genug Platz für die Krebszellen sein, die durch das Konstrukt reisen und sich an die anderen Zellen anhaften.
Das Problem hat viel mit Porosität, Diffusivität, Biokompatibilität und Bioabbaubarkeit zu tun, alles Materialeigenschaften. Ein Großteil des Projektes ist also ist eine Polymerforschung.
Es ging auch viel um hochauflösenden 3D Druck: Die Porosität kann durch präzise Geometrie eingestellt werden. Ein Problem, an das man anfangs nicht denkt, taucht auf, wenn man die Porosität homogen über den Chip verteilt. Wenn die Zelle in das poröse Medium eintritt und nicht genug Geschwindikeit hat, kann es passieren, dass man den Chip blockiert. Er ist dann einfach verstopft wie ein verstopfter Abfluss. Jedoch kann die Zelle auch nicht beliebig schnell in das Medium eintreten, da sie das Medium passiert, ohne sich anzuhaften. Man muss die Umgebung also so gestalten, dass sie afangs eine höhere Geschwindigkeit erlaubt als am Ende. Ein Porositätsgradient (sinkende Porosität vom Beginn bis zum Ende der Struktur) kann die Wahrscheinlichkeit für die Zellanhaftung erhöhen. Das konnten wir teilweise über Materialeigenschaften und teilweise über Geometrie einstellen.
Ich bin noch immer involviert. Ich habe einen Post-Doc, der noch in Norwegen arbeitet, mit dem ich wissenschaftlich über diese Themen referiere.
Weil Sie nach dem INCITE-Projekt und Brennstoffzellen gefragt haben: Bei beiden muss ich entsprechende Transportwege zur Verfügung stellen, den Massentransport optimieren. Haben Sie schon einmal die IV-Curve einer Brennstoffzelle gesehen?
Reisswolf: Nein.
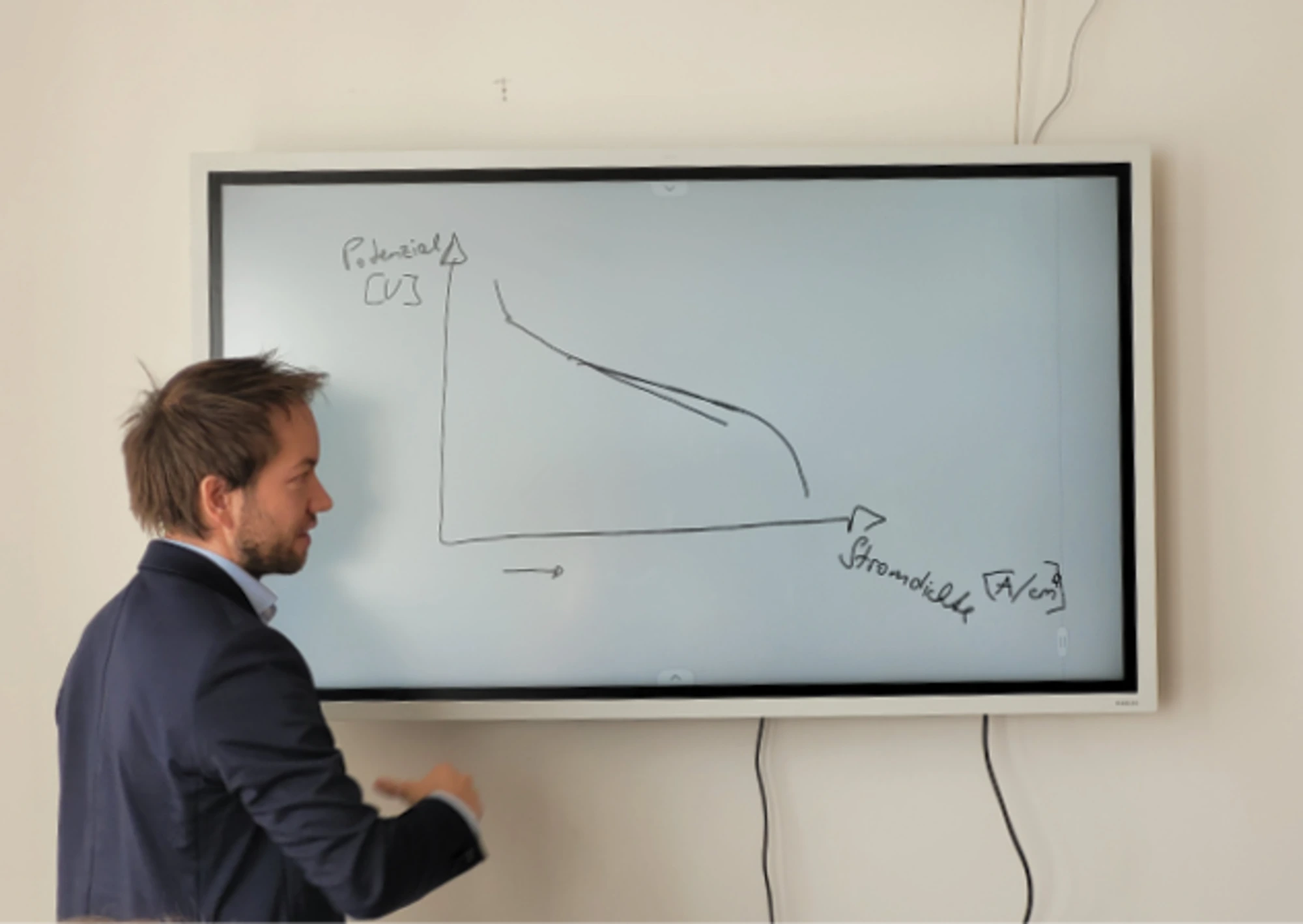
Professor Torgersen: Ich zeichne es Ihnen auf. Wenn Sie eine IV-Curve anschauen, haben wir Stromdichte in Ampere pro Quadratzentimeter auf der x-Achse und hier haben wir Potential in Volt auf der y-Achse. Dann haben Sie klassischerweise einen solchen Verlauf wenn Sie eine Last auf Ihrer Brennstoffzelle auflegen: Mit steigender Stromdichte sinkt das Potential zunächst mal schnell ab, das sind Aktivierungsverluste. Die hängen mit dem Katalysator zusammen. Der zweite, lineare, Bereich hat mit der Leitfähigkeit (dem elektrischen Widerstand) zu tun. Je geringer die Leitfähigkeit, desto steiler diese Kurve. Je dünner zum Beispiel diese Brennstoffzelle ist, desto besser, desto flacher ist die Kurve, weil der Strom nicht weit fließen muss. Und dann hat man den rechten Bereich, in dem die Kurve steil abfällt. Das ist der kritische: dort sind die Massentransportverluste. Es gibt hier eine Asymptote, die die Grenze der Belastbarkeit der Brennstoffzelle darstellt.
Und wenn wir jetzt natürlich in die Zukunft denken, wir wollen mit kleineren Zellen mehr Wasserstoff, als mehr Leistung, oder einfach eine höhere Ausbeute an Wasserstoff, an einem Elektrolyseur, dann müssen wir den dritten Abschnitt der Kurve nach rechts verschieben. Da ist die Frage, wie kriegen wir den Massentransport in diesen Zellen gut hin? Natürlich, wir sind alle CAD-Experten und wir können alle super FEM simulieren. Jetzt müssen wir aber auch die Möglichkeit haben, optimierte Geometrien da reinzubringen. Und das hoffen wir eben mit dem Prozess zu können.
Deswegen haben mich diese Leute von dem INCITE-Projekt auch angesprochen, weil sie die Transporteigenschaften in einer Matrix einstellen wollen. Wir brauchen im Endeffekt eine hohe Perfusion, wir brauchen eine hohe Leistungsfähigkeit dieses Mediums beim Durchtransport. Nicht von Wasserstoff oder Gasen, sondern von Zellen, von Kugeln in einem Medium sozusagen. Deswegen mag das vielleicht ein bisschen weit weg klingen, aber wenn man genauer hinschaut, ist es ein ähnliches Thema. Ich hätte es auch nicht gedacht.
Reisswolf: Haben Sie schon mal darüber nachgedacht, Richtung Industrie zu gehen oder wollten Sie immer lehren? Oder hat sich das einfach so ergeben?
Professor Torgersen: Ja, ich hatte mehrere Möglichkeiten dazu. Während meiner Doktoratszeit sind drei Firmen aus meiner Gruppe in Wien entstanden, die jetzt am 3D-Druckmarkt sehr bedeutend sind. Da hätte ich einsteigen können. Aber mich hat es immer interessiert, in der Wissenschaft zu bleiben und wissenschaftliche Fragestellungen zu beantworten.
Lehre habe ich erst in Stanford gehalten, da habe ich die Vorlesung „Fuel Cell Fundamentals“ gehalten. Eigentlich bin ich über die Lehre erst zu diesen Themen gekommen. Lehre finde ich ausgesprochen wichtig. Gute Lehre ist die Essenz für den wichtigsten Output einer Universität: die Absolventinnen. Eine Universität hat die gesellschaftliche Verantwortung, die Absolventinnen mit dem notwendigen Wissen auszustatten, um als Ingenieure etwas bewirken.
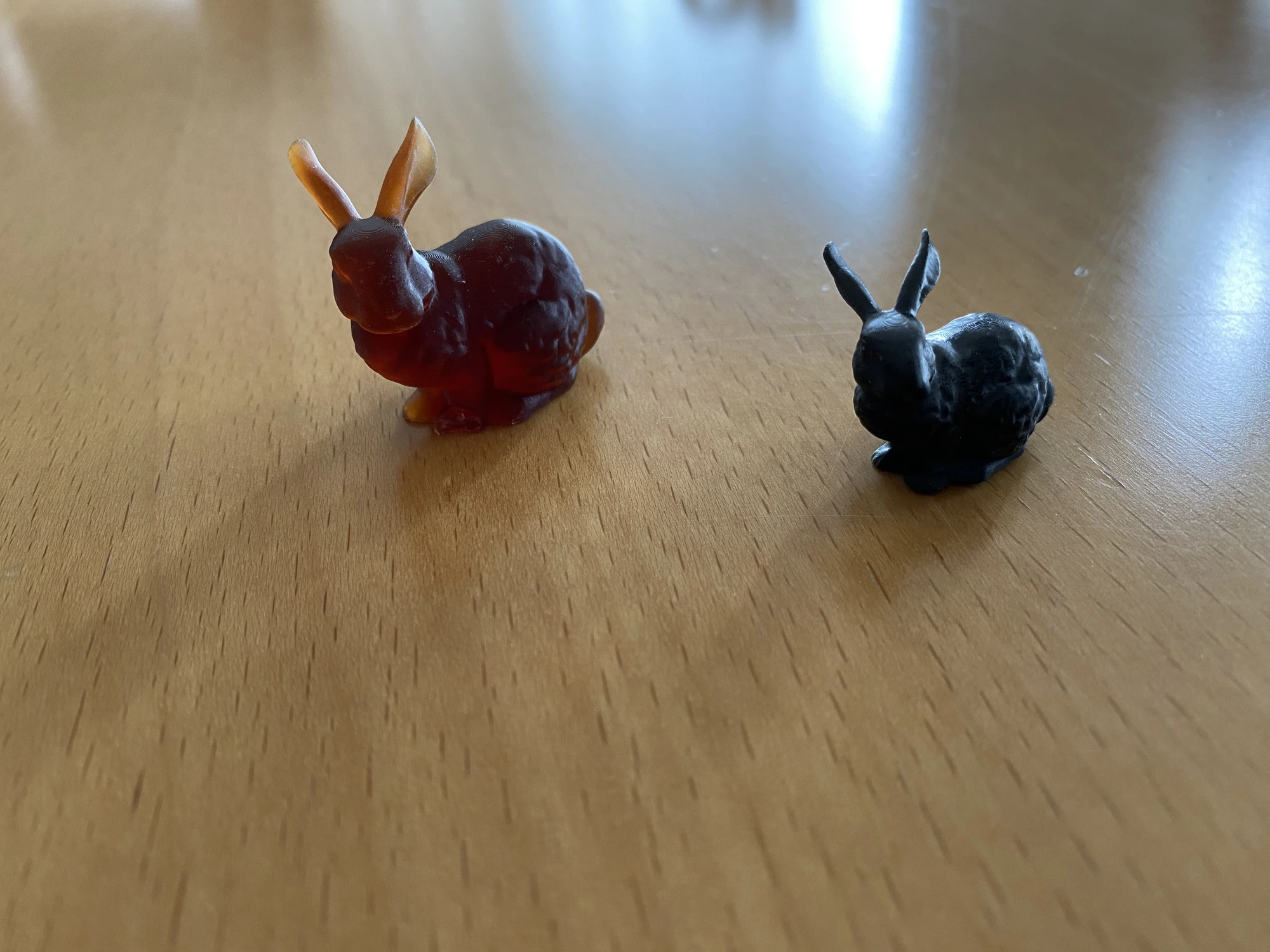
0 Kommentare