Towards a fully renewable future energy mix
Wind energy has become one of the principal sources of renewable energy in the world, and it is expected to play an ever-growing role in the transition away from fossil fuels. The success of wind energy is primarily due to the great progress made in the last decades in understanding the complex physical phenomena that underlie the process of energy conversion from wind, and translating this knowledge into sound technical solutions. Notwithstanding the recent advances, there are still many scientific and technological challenges that need to be overcome, in order to increase the penetration of wind, reduce its cost and mitigate its impacts. To contribute to the achievement of these goals, the Wind Energy Institute at TUM works on basic scientific and application-oriented problems, often in close collaboration with industry. Areas of specific expertise of the Institute embrace all main wind-energy-relevant scientific disciplines, including aerodynamics, structures, dynamics, materials, and controls with a strong focus on multi-disciplinarity and a systems-engineering point of view. Some of the most exciting ongoing projects at the Institute are briefly described in the following.
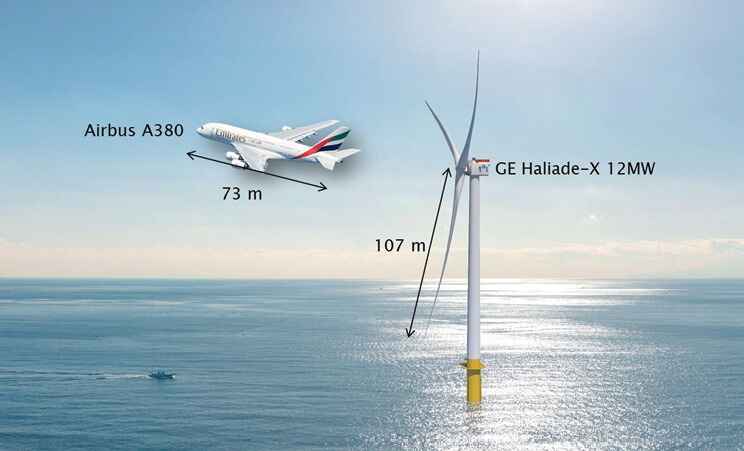
Design of Wind Turbines
The design of wind turbines is an extremely complex multi-disciplinary activity. In the design process, one must be able to find the best possible compromises from different and often contrasting requirements. In addition, multiple aspects of the problem have profound and complex couplings, including the aerodynamic and structural designs, the control laws used to govern the machine, and the performance and characteristics of all on-board sub-systems. To address these challenges, we develop automated design procedures implemented in sophisticated software tools, which are capable of performing the integrated aerostructural design of a complete wind turbine. Using these tools, WEI researchers work on answering the following and many other fascinating questions:
What are the optimal machine sizes and configurations for a given application?
What are the impacts and possible benefits of new technologies, as for example passive and active load alleviation methods? And what are their costs and drawbacks?
Are new wind turbine configurations competitive with standard designs, and if so, for which applications? Is there any advantage in downwind, free-yawing machines, pre-aligned rotors, active flaps or in the use of unconventional techniques such as active coning and morphing rotors?
Will future extremely large blades look similar to the current ones, or are there better and possibly radically different ways of designing blades?
How can we hedge against the myriad uncertainties that plague the design and operation of wind turbines and farms? How can we achieve more robust designs and reduce safety factors?
Control of Wind Turbines and Wind Farms
Control technology holds much promise for improving the way wind turbines and wind farms are operated, and may contribute significantly to reducing the cost of energy from wind. In fact, as sensors become cheaper and more capable, digital controls can make existing and future assets “smarter”, optimizing the way turbines and farms respond to complex inputs and behave in challenging operational scenarios. These are some of the most interesting and pressing scientific questions we are working on:
- How can we improve the way wind turbines are controlled, to increase power capture and/or decrease loading to extend life?
- Can we move away from the greedy control approach used today on board wind turbines, where each turbine is operated individually with little or no consideration of what neighboring machines are doing?
- What can be gained by using cooperative control strategies of wind turbines within a farm? By the use of cooperative control, can we mitigate wake losses or reduces loading? Does the use of smart cooperative control lead to new ways of designing future wind farms? And, by cooperative control, can we also improve the way existing wind farms operate today?
- Can we operate wind farms more similarly to what is done for other conventional energy sources, and can this help in the integration of a higher share of wind in the energy grid?
- What knowledge on the wind and the system response is necessary to enable smart control approaches for turbines and farms? And what sensors can provide such information at a low cost, high availability and moderate complexity?
Wind Sensing Technology
At present, wind turbines are largely unaware of the wind blowing on their rotor: they are equipped with anemometers and wind vanes installed on the nacelle, which only measure wind speed and direction at that point in space. Therefore, wind turbines are essentially operating in the dark: they have only a very primitive knowledge of the atmospheric conditions, and they ignore whether or not they are shaded by other machines. This lack of awareness clearly hinders the way they are operated.
We are working on changing this situation, developing new technology that can measure the wind conditions at the rotor disk. This is achieved in a radically new way: turning the whole rotor in a large wind sensor, a novel approach that we have termed “wind sensing”. By the use of wind turbine response data, wind sensing technology computes the wind conditions at each machine. In turn, better knowledge of the wind is used for an improved operation of each wind turbine or the whole wind farm by smart control strategies.
Recently, we are also exploring other digital applications empowered by wind sensing, related to predictive maintenance, lifetime consumption estimation, digital-twin technology and wind forecasting.
These are some of the key scientific questions we are working on:
- What wind characteristics can we measure and with which precision?
- What is the minimum set of sensors that are necessary for measuring the wind inflow?
- What is the use that can be made of detailed wind information at the rotor disk?
- What new control approaches can be developed based on wind sensing technology? How can wind sensing improve the way a wind turbine is controlled? And how does wind sensing enable smart wind farm control methods?
- What other digital applications can be supported by wind sensing?
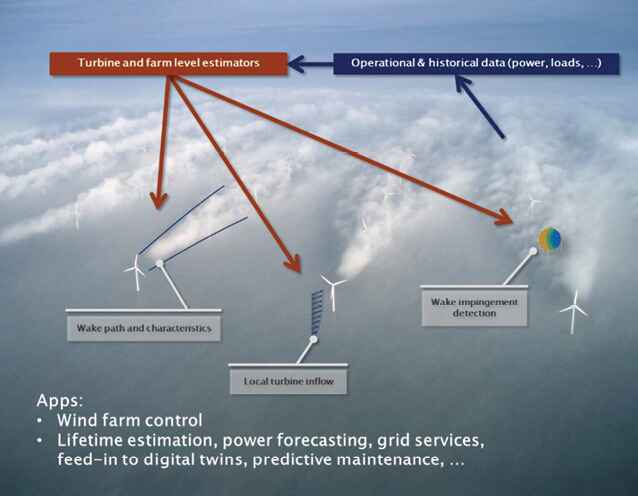
Experimental Testing
Experimental testing is crucial for verifying and validating the results of all our research efforts, including mathematical models, simulation tools, control strategies or new technologies. Testing in the field on production machines is however very challenging, possibly expensive and often altogether impossible. To address some of the limits of full scale testing, WEI has developed new technology for scaled model testing in boundary layer wind tunnels. These are some of the most important research questions that WEI researchers are trying to answer:
- Can we replicate in the controlled environment of a wind tunnel some of the key physical aspects of the energy conversion process from wind? How should scaled models be designed in order to match as many of the relevant physical parameters as possible?
- Can we faithfully replicate wake behavior, wake interactions, and complex terrain effects?
- Can we go beyond the matching of purely aerodynamic effects, replicating at scale also the aeroservoelastic behavior of wind turbines?
- Can closed-loop control methods for wind turbines and farms be tested at scale? If so, what do we capture with good precision, and what are the limits of these scaled models with respect to full-scale reality?
Our scaled models are miniaturized wind turbines and, exactly as full-scale machines, they are governed by closed-loop pitch, torque and yaw controllers. Optionally, a super-controller can be used for the collective control of clusters of wind turbine models, enabling the study of wind farm control techniques. Our family of wind turbines includes at present three different sizes: the largest models (termed G2, with a 2 meter rotor diameter) can be optionally equipped with aeroelastically scaled blades, while the smaller ones (G1 and G0.6, of 1 and 0.6 meters of diameter, respectively) are used for modeling wind turbines clusters, studying wake interactions and complex terrain effects. A high-fidelity digital copy of the models and the wind tunnel has been developed by WEI researchers, using state of the art CFD techniques coupled with aeroelastic wind turbine models. The experimental results are used to validate the digital models, which in turn are used for studying wakes, turbulent flows within wind farms and wind plant control, as well as for the planning of future experiments.
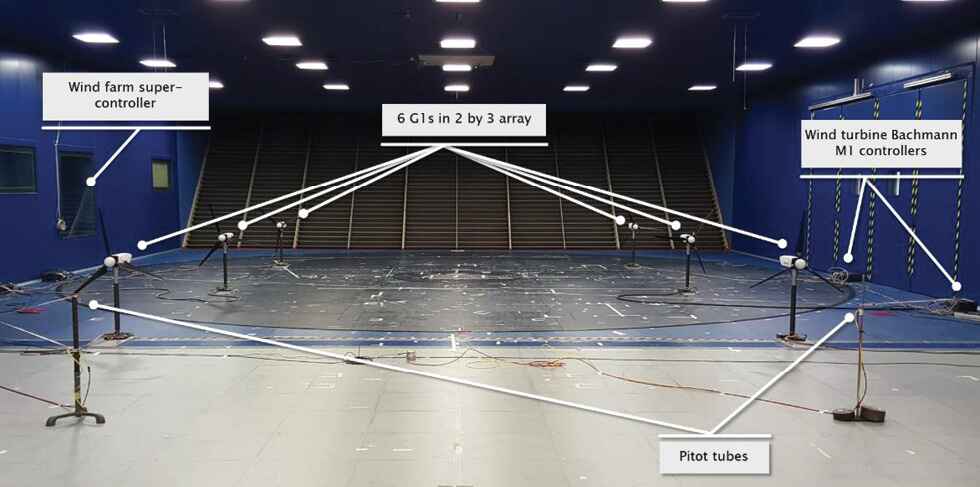
Experimental activities at WEI are not limited to scaled testing. In fact, within a joint project with the research cluster WindForS (Windenergie-Forschungscluster), we are working on the development of an experimental test site in complex terrain. The test facility, funded by the Federal Ministry for Economic Affairs and located in Baden-Württemberg, will include two highly-instrumented 750 kW wind turbines, as well as extensive instrumentation for the measurement of wind conditions. Once operational, the test site will enable new exciting and unique testing capabilities, paving the way for an improved understanding of wind conditions and the optimization of wind turbines for complex terrain applications.
0 Kommentare