A series of beyond 3D printing
Author: Kaavya Ramachandran
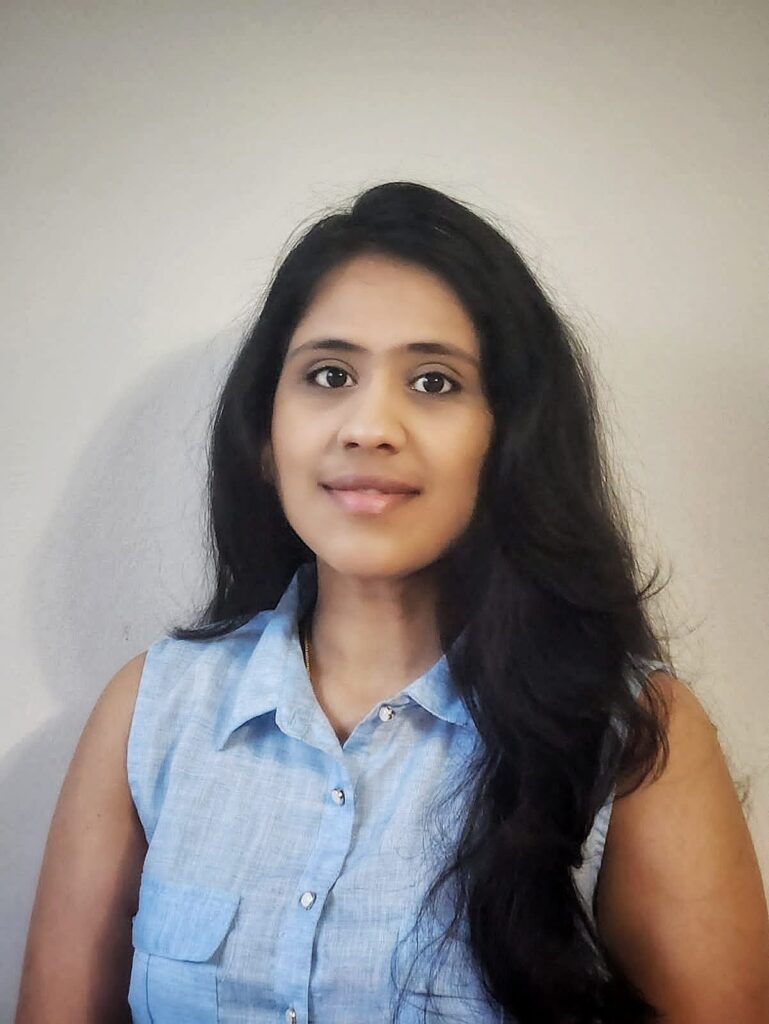
Person interviewed: David Wenzler from Institute of Machine Tools and Industrial Management (iwb)
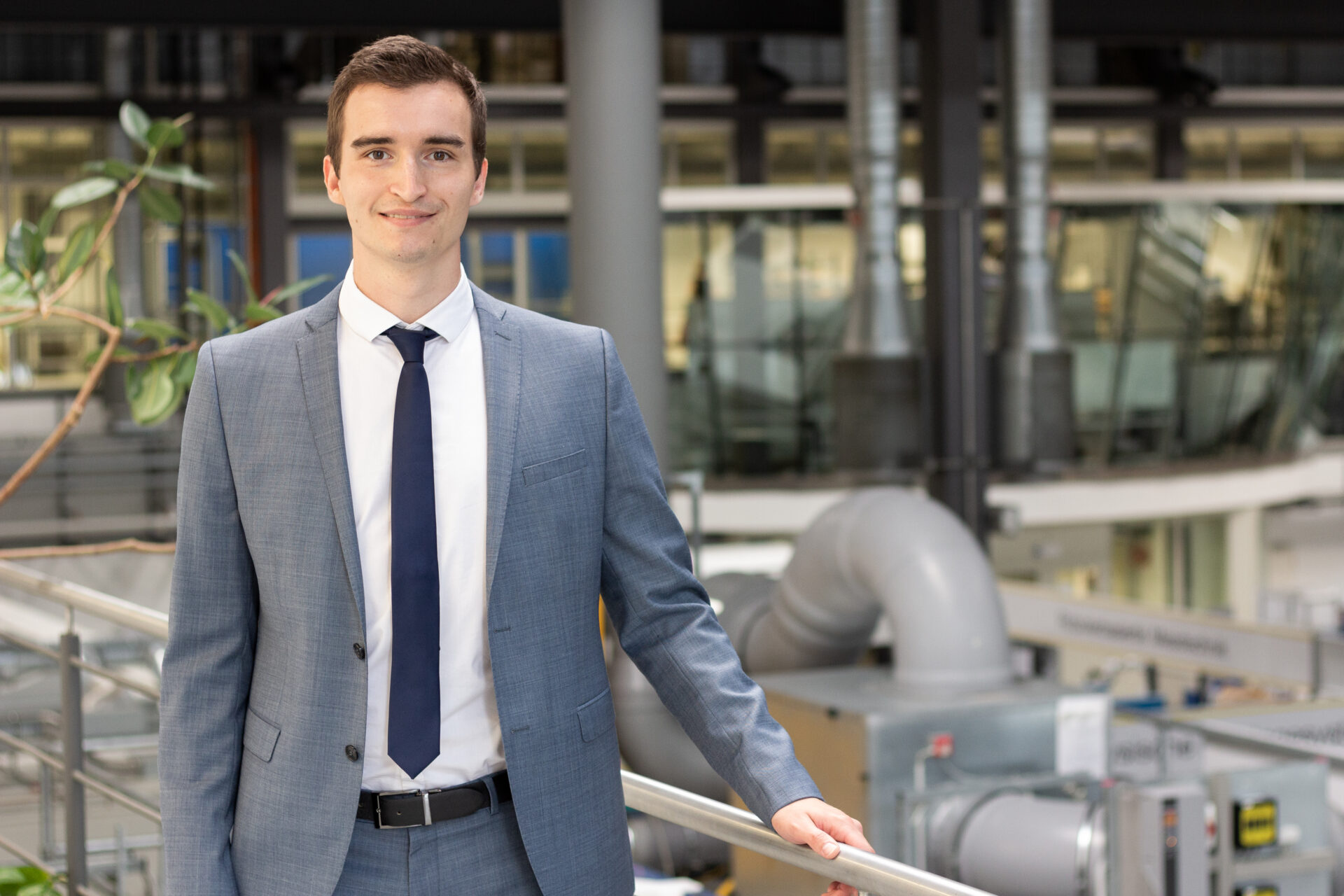
Can you elucidate the operational intricacies of the powder bed fusion technology?
David Wenzler: Powder bed fusion of metals using a laser beam (PBF-LB/M) harnesses the transformative potential of metallic powders to reshape manufacturing frameworks. Metallic powder, as the feedstock material employed in this process, is delicately spread over a build plate using a recoating or coating system. A steel plate, typically around 40 millimeters in height, acts as the build plate. In our setup, a conveying belt dispenses the powder from the top, then a knife-like blade levels the powder layer precisely. This ensures a smooth, uniform surface for the process. The layer height typically ranges between 20 to 80 µm, with metallic powders featuring a fine particle size distribution, usually around 40 to 50 µm. Now, let’s talk lasers. A scanning device equipped with mirrors directs the laser beam to selectively melt areas of the powder bed, layer by layer. This ensures an optimal bonding between layers. After each layer is scanned, the build plate descends by one layer height, usually around 40 µm, and a new layer of powder is coated. This iterative process continues until the desired object is fully formed within the chamber. Once completed, the excess powder is removed, revealing the finished product. After cutting it off the build plate the component is ready for use or further processing steps. Often post-processing such as tsupport structure removal, surface finishing, or heat treatment is needed.
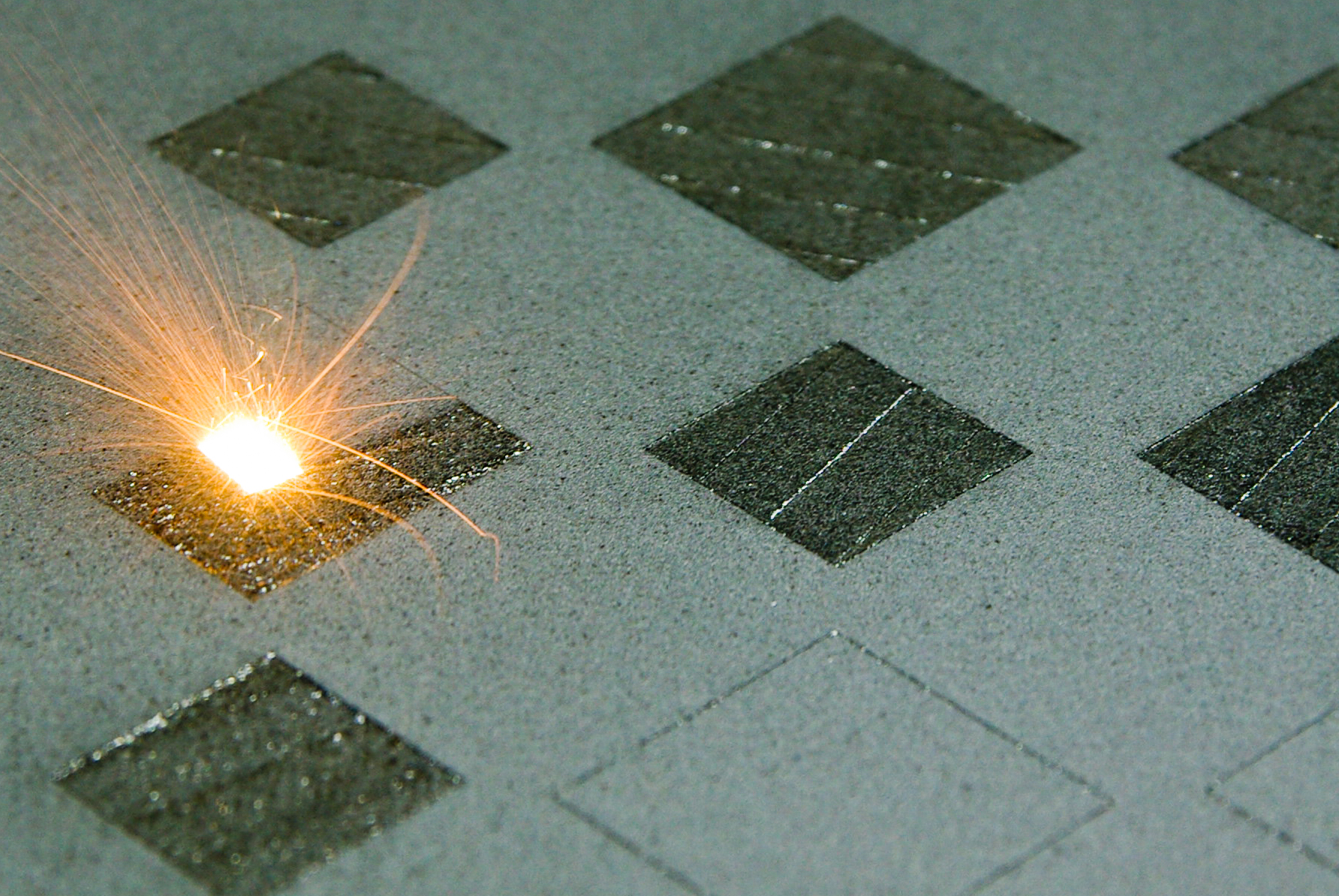
What are the essential safety precautions during this manufacturing method?
To ensure safety when using this process, it’s crucial to recognize the hazards associated with the powder and the laser used. Working in an enclosed environment is imperative to contain the powder. At the iwb, there is a separate lab with a sealed and controlled environment. Regular cleaning procedures are implemented to prevent the powder from dispersing throughout the workspace. To protect the user from the laser beam, an enclosure is part of the machine.
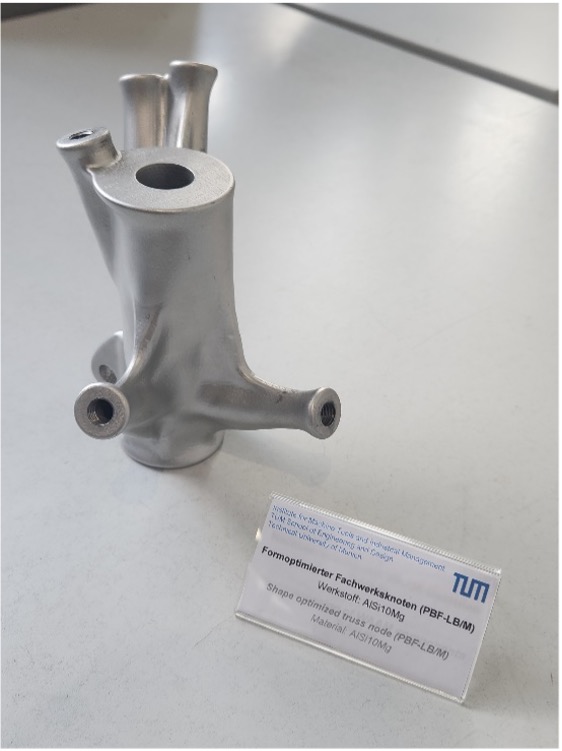
What materials are typically used in additive manufacturing?
The most commonly used metals in additive manufacturing include Titanium alloy TI6Al4V, Aluminum alloy AlSi10Mg, 316L stainless steel, and Inconel 718. Recently, new powders such as Scalmalloy have gained traction in the field. In the past, even gold was used.
Can you provide examples of parts or components manufactured using this method that are commonly encountered in everyday life?
Absolutely! Examples of components crafted through this innovative technology , frequently seen in daily life, encompass fuel nozzle injectors by GE Aviation, baroscopic eye examination devices, window guide rails manufactured by BMW for the i8 Roadster, and optimized pistons developed by Porsche.
Do you know? You can check the interesting projects @ Startseite – Institut für Werkzeugmaschinen und Betriebswissenschaften (tum.de)
What research projects are happening at the Institute of Machine Tools and Industrial Management (iwb)?
The KREATIVE project combines various additive manufacturing technologies to optimize production and resource efficiency by utilizing different processes for producing components with intricate details and larger sections. Within the Collaborative Research Center TRR 277 (Additive Manufacturing in Construction), there is also research about combining two manufacturing methods: drawn-arc stud welding with Wire and Arc Additive Manufacturing (WAAM), resulting in stud and wire arc additive manufacturing (SWAAM). This increases the production rate of geometrically complex large-scale lattice structures. Another focus of the iwb within the Collaborative Research Center lies on exploring and evaluating the factors influencing the manufacturing of safe and durable structural steel elements by PBF-LB/M. The relationships between process parameters, the cooling rate, the post-treatment and geometric aspects with the static and cyclic mechanical properties of PBF-LB/M-manufactured steel components are determined. Based on these findings, design recommendations were derived to manufacture steel components with reproducible and defined mechanical properties.
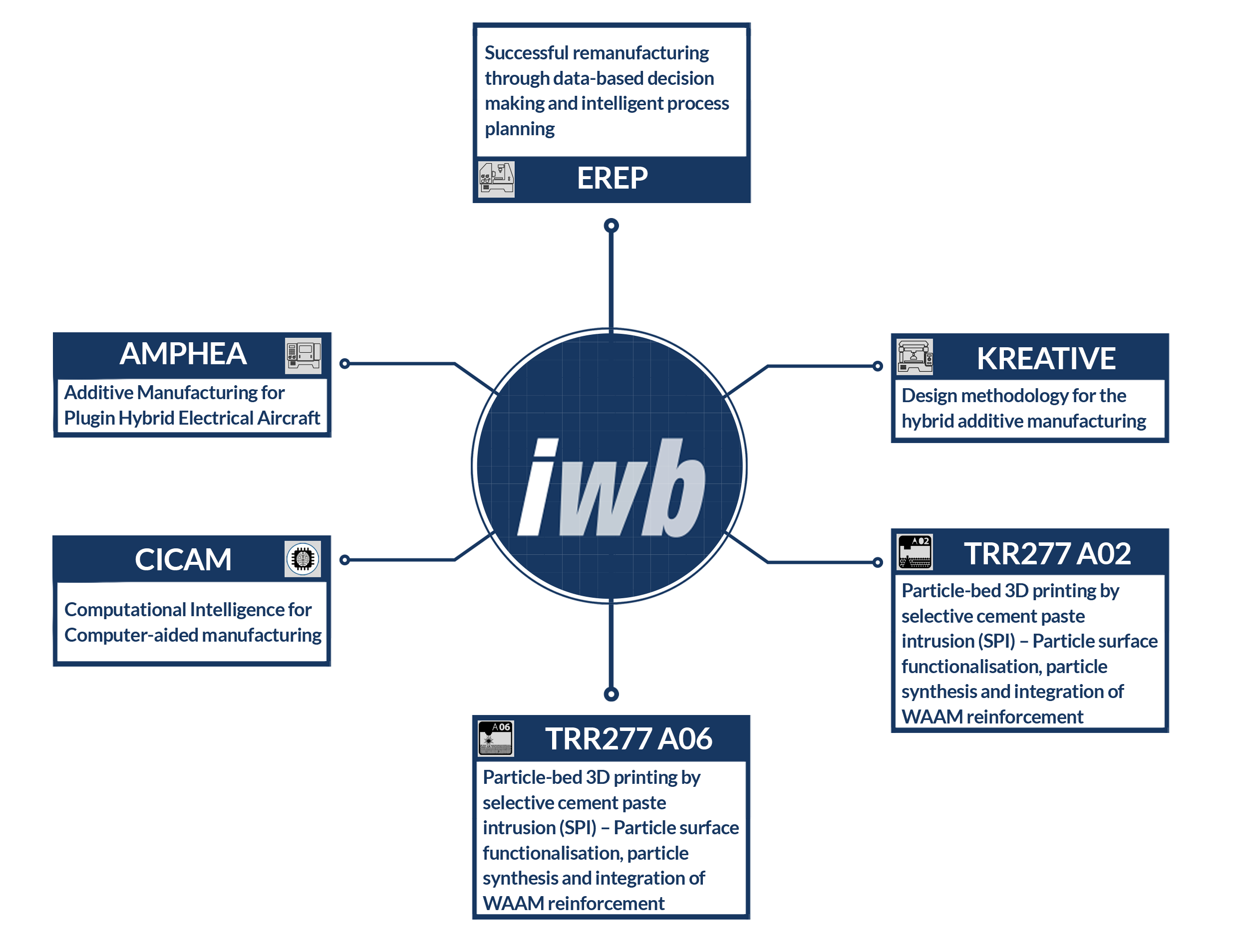
Additionally, the now completed project Ascent AM aims to predict parts‘ thermal and mechanical behaviors, enabling proactive CAD geometry adjustments to mitigate post-production deformations. The range of research at iwb is quite broad.
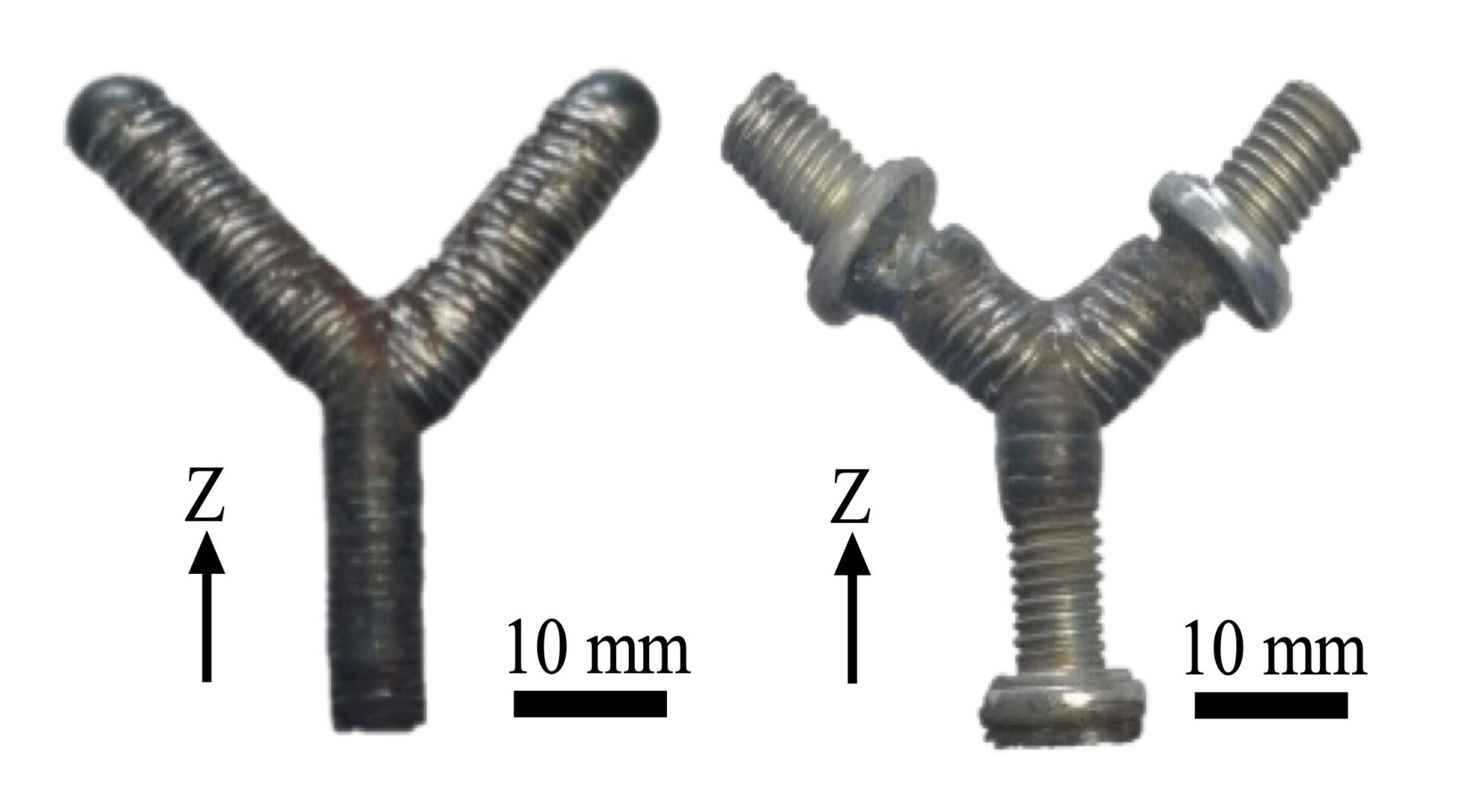
a) structure produced with the WAAM process, b) structure produced with the hybrid SWAAM process
What are the pros & cons of powder bed fusion to conventional manufacturing methods?
Powder bed fusion offers several advantages to conventional manufacturing methods. It provides a high accuracy and an intricate geometrical complexity, coupled with the ability to work with a diverse range of materials, including various steel alloys, aluminum alloys, and titanium alloys. Despite its slow build rate and size limitations compared to machining for example, powder bed fusion allows for the reuse of powder and, therefore, reducing waste.
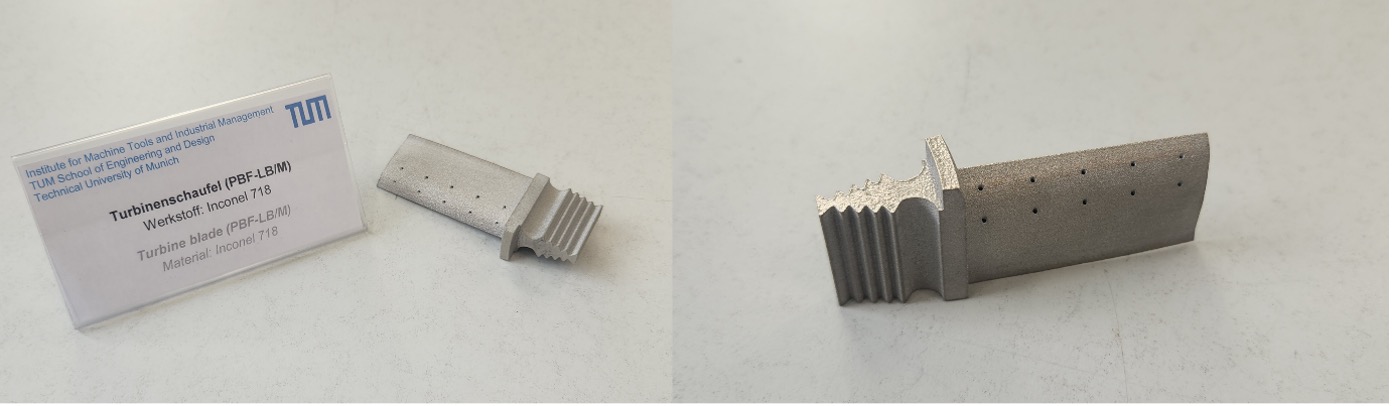
How is rough surface finishing handled in the manufacturing process?
To address the rough surface finishing, we employ various surface treatments tailored to the specific needs of each part. Sandblasting is effective in removing excess sintered powder from the surface, offering a cost-effective and straightforward solution. Alternatively, vibratory grinding, involving a tumbler with grinding particles, ceramics, and liquid, smoothens the surface over hours or days. There is also this post-processing solution of 3D printed metal parts called Hirtisation®. It uses a combination of electrochemical pulse methods, hydrodynamic flow and particle assisted chemical removal with no mechanical processing steps involved. An acid treatment process is utilized for internal channels that vibratory grinding cannot reach.
Are there alternative methods akin to powder bed fusion, serving as parallel concepts, derivatives, or advancements in the field?
PBF-LB/M employs a laser beam as the energy source to melt the powder, while a parallel concept, powder bed fusion of metals using an electron beam melting (PBF-EB/M), utilizes an electron beam for the same purpose. In PBF-LB/M, a shielding gas atmosphere is required during the laser welding, whereas PBF-EB/M necessitates a vacuum environment due to the absence of atoms in the atmosphere. These differences stem from the distinct melting sources and influence certain features of the machines.
At the iwb you even build your own device to dive deeper into the process?
Exactly! At our chair there is a specific setup, referred to as the Laser Beam Manufacturing Chamber, developed by my colleague during his PhD project. It operates similarly to PBF-LB/M machine but on a smaller scale. At the top, the laser deflection optics are positioned, allowing for precise control of the laser’s path. The laser is not enclosed within a casing.For this reason, the machine is placed in a laser safety cell at the institute. The setup includes sensors to monitor the process, aiding in the validation of simulations and the testing of hypotheses. In a 2021 publication, we demonstrated the effectiveness of this setup by correlating sensor data with indicators such as spatter creation and changes in the melt pool intensity, identifying occurrences of defects during the process. This work showcases the potential of this method derived from powder bed fusion for advanced monitoring and analysis in additive manufacturing.
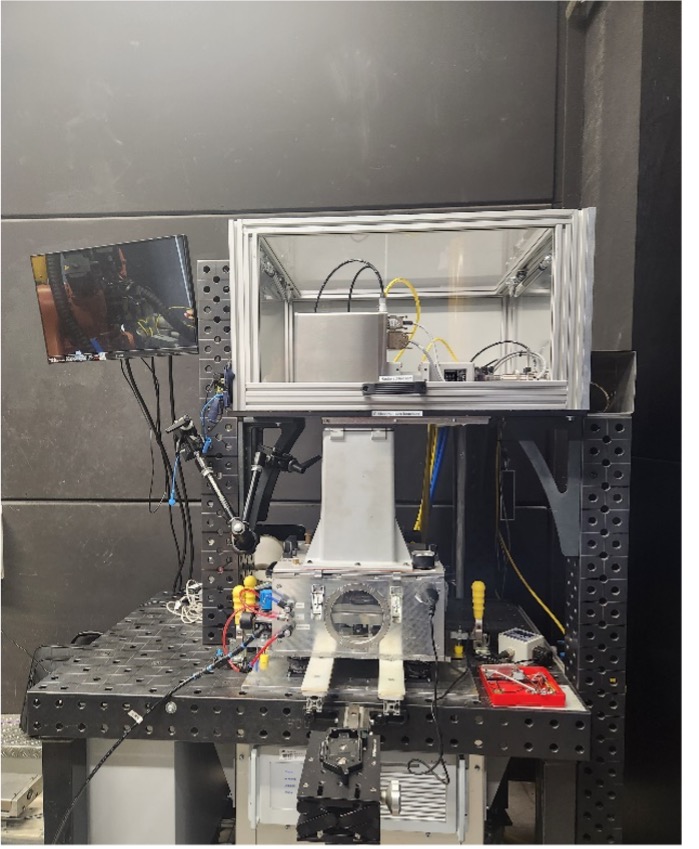
Our project reAM250 aims for a research system for PBF-LB/M, that is open-source and especially tailored for research on process monitoring and control. With active student involvement, it offers hands-on experience across hardware design, process development, and software creation. This interdisciplinary initiative allows students to explore mechanical engineering, electronics, software development, and automation. Through thesis work, students contribute to advancing knowledge and gain practical experience in real-world research settings. Join us for a dynamic research opportunity to make meaningful contributions and foster critical skills.
0 Kommentare