A new era of Additive Manufacturing concepts for high-performance parts
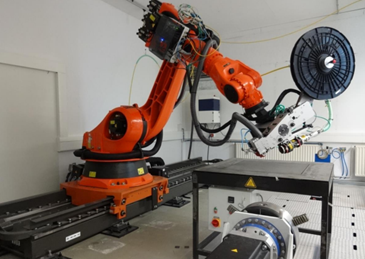
Automated Fiber Placement is a cutting-edge AM technology that has revolutionized the production of composite materials, particularly in the aerospace industry.
By now, everyone is familiar with FFF printing and many also have an FF printer at home. But what else is and can additive manufacturing actually do? Fabian Diemar at the Chair of Carbon Composites (LCC) at the TUM School of Engineering and Design heads the topic field for Automated Fiber Placement (AFP) at the Technical University of Munich (TUM). Fabian and his group of researchers focus on the advancement of AFP technologies for manufacturing state-of-the-art lightweight components made of CFRP contributing towards sustainability by reducing carbon footprint and energy consumption.
Decoding AFP: How does it work?

AFP is a highly automated manufacturing technology that utilizes industrial robots to place composite prepreg slit tapes onto molds. The process involves shaping the raw material, which consists of carbon fibers embedded thermoset or thermoplastic matrix. The robot-mounted placement head lays the material layer by layer according to the desired fiber direction, creating strong and lightweight composite components. An autoclave curing process is required for certain materials, whereas for Automated Fiber Placement (AFP) using in-situ consolidation with thermoplastic (TP) tapes, the layers are fused together during placement, eliminating the need for subsequent post-curing procedures.
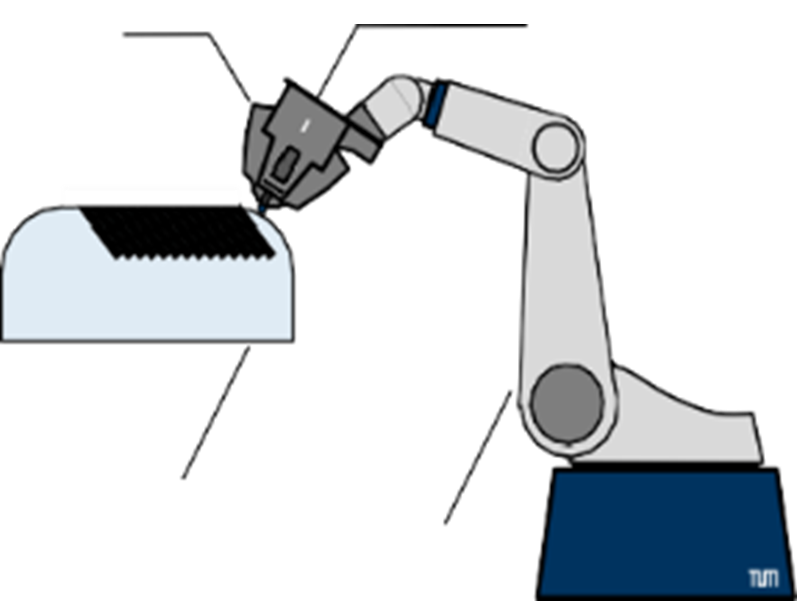
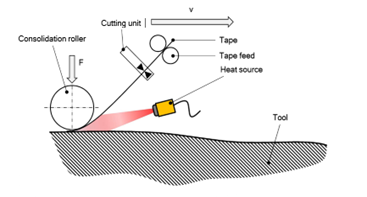
AFP vs. Traditional Manufacturing
AFP technology enables the accurate placement of fibers layer by layer, ensuring consistent fiber orientation and minimal material wastage.
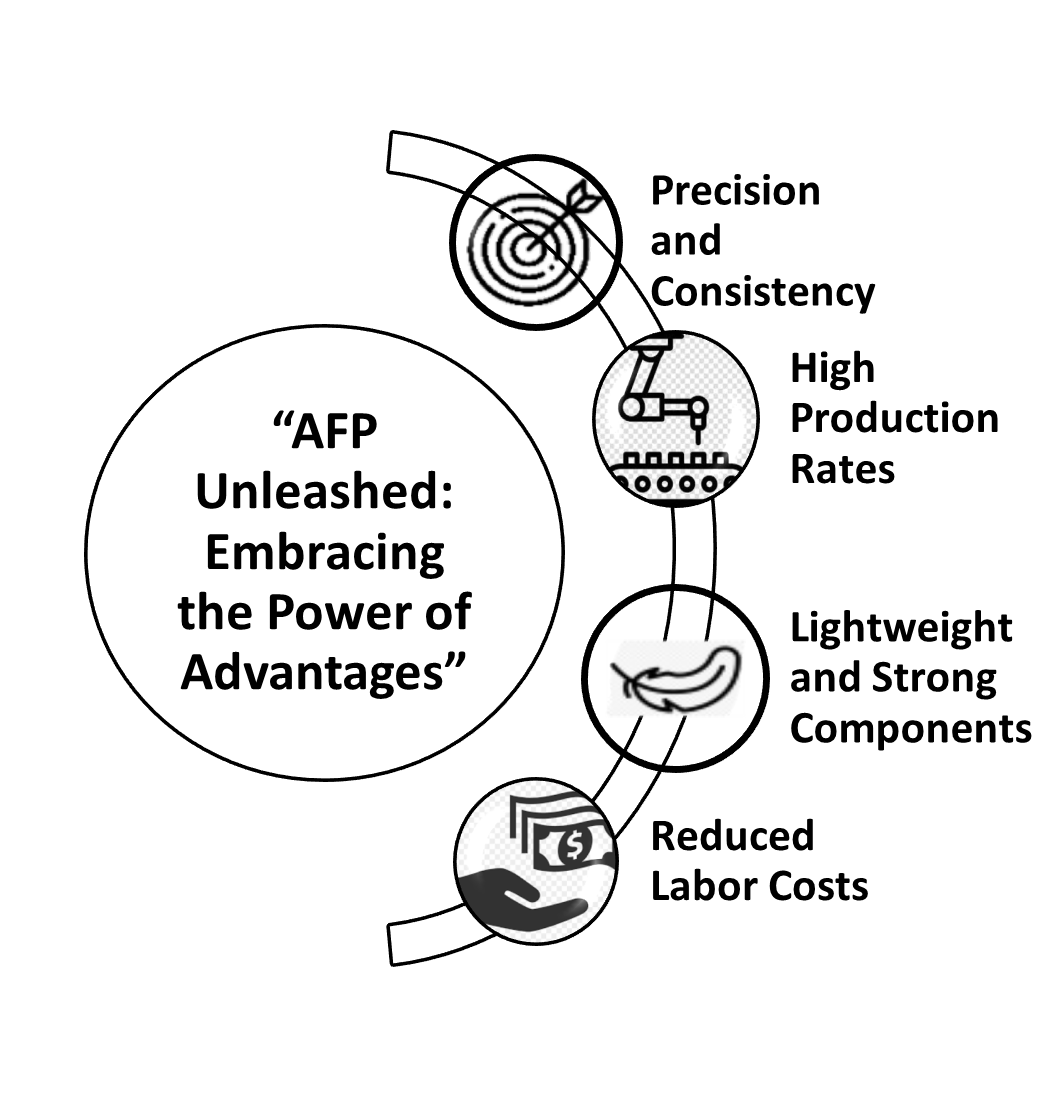
The robotic system allows for complex geometries, making it ideal for aerospace components, turbine blades, and pressure vessels.
Composites produced using AFP have excellent strength-to-weight ratios, and eliminate the need for manual labour, reducing production costs, and the potential for human errors.
AFP allows designers to tailor the orientation of fibers to suit specific load requirements, resulting in optimized composite structures with enhanced mechanical properties.
Components Manufactured by AFP at LCC: From Pressure Vessels to Rocket Fairings
AFP is used to produce a wide array of components, such as aircraft wings, fuselage sections, helicopter blades, rocket fairings, pressure vessels, and automotive parts. Its ability to create complex shapes and optimize fiber orientation makes it ideal for critical and lightweight structures.
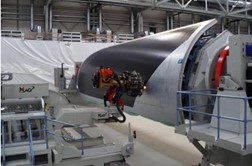
At LCC, our researchers are actively engaged in the advancement of aerospace applications through the development of door frames utilizing sandwich structures, fabrication of intricate three-dimensional components and are committed to the ongoing enhancement of pressure vessels for the promotion of sustainable aviation.
Significance of Fiber Orientation in AFP
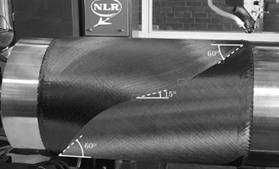
Fiber orientation plays a crucial role in determining the mechanical properties of composite materials. AFP allows precise control over Fiber orientation, enabling engineers to tailor composite components for specific load requirements. Proper Fiber alignment enhances the strength and stiffness of the final product, making it essential in aerospace and other high-performance applications.
How do winding process patterns affect AFP manufacturing?
Winding process patterns dictate the path of the AFP head as it places the fibers onto the mold. The patterns can be optimized to minimize gaps, overlaps, and weak spots in the composite structure, ensuring uniform distribution of fibers for enhanced strength.
Diverse Materials in AFP: Beyond Carbon Fibers
AFP is compatible with various composite materials, including carbon fibers, glass fibers, aramid fibers, and hybrids. These materials offer a range of mechanical properties, thermal resistance, and cost factors, allowing manufacturers to choose the most suitable material for a particular application.
„Breaking Boundaries, their Research Ventures into Four Thriving Techno-Realms!“
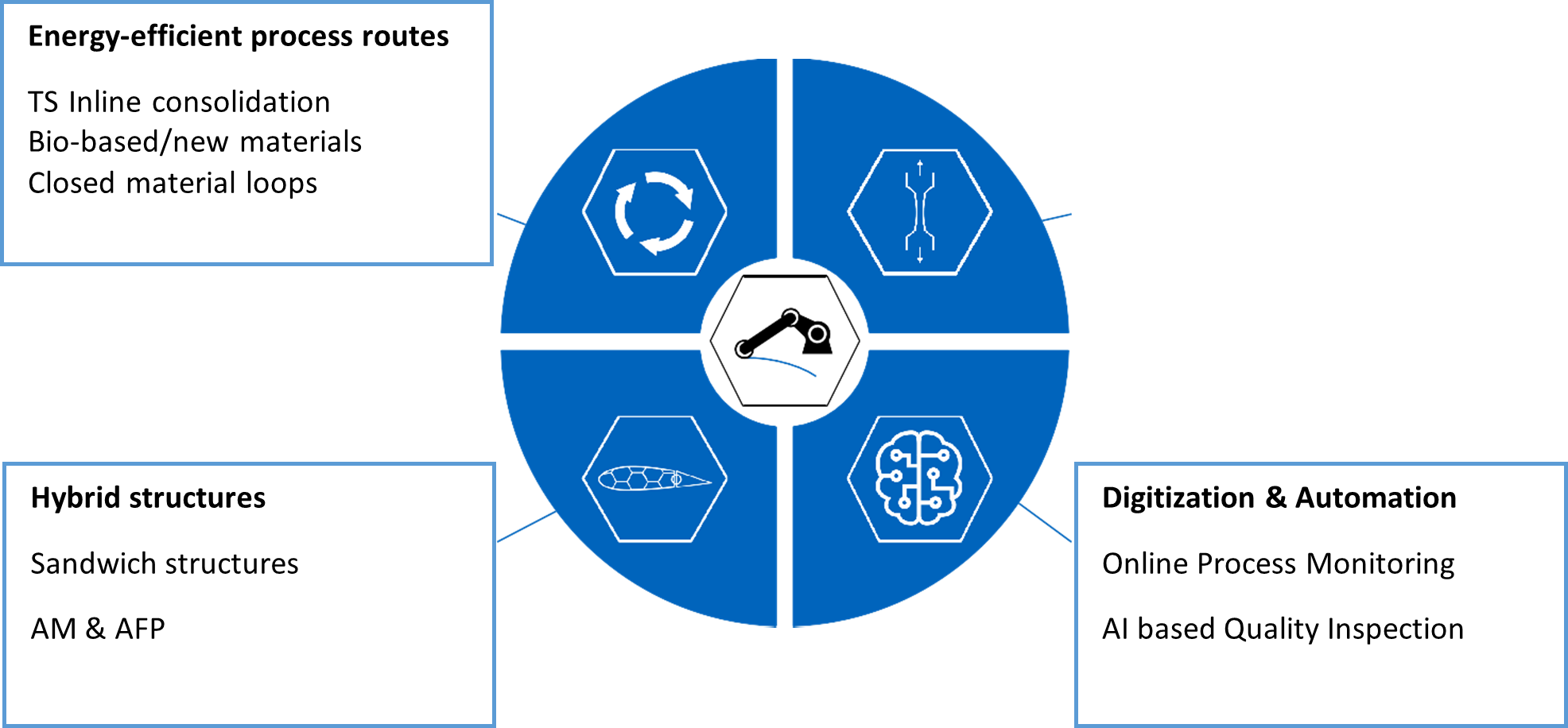
Energy-Efficient Process Routes:
The team is dedicated to reducing manufacturing processes‘ energy consumption and carbon footprint. They explore alternative manufacturing technologies to avoid energy-intensive autoclave curing methods commonly used in thermoset AFP. Sustainability is a key focus, and the team is working on adapting processes to optimize energy efficiency.
Material Characterization:
In this field, the researchers investigate material properties related to AFP. They study the prepreg material, cured material, and process parameters using different test benches. Understanding material behaviour is crucial for ensuring the quality and performance of AFP-produced components.
Digitalization and Automation:
The team is developing frameworks for online process monitoring, integrating sensors to monitor the AFP process and product quality. Artificial Intelligence (AI) plays a significant role in detecting defects, and anomalies, and ensuring the quality of the final product.
Hybrid Structures and 3D Printing Integration:
Researchers are exploring the combination of 3D printing and AFP technologies, aiming to leverage the advantages of both methods. Hybrid structures offer enhanced performance and increased design flexibility making them suitable for various applications.
Advancements in AFP Technology Unleash
Digitalization and AI Integration: Implementing AI-based quality inspection systems to automatically detect defects and ensure consistent product quality.
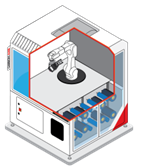
Readiness Level for Thermoplastic AFP: Advancing the readiness level of thermoplastic AFP to make it more viable for industrial applications.
Modular Tool Integration: Developing modular robot heads to combine different manufacturing technologies, enabling more efficient and cost-effective processes.
Diversification of AFP Applications: Exploring new markets outside of aerospace, such as sports products, automotive, and agricultural machinery, to increase the application scope of AFP.
Challenges in AFP
- Programming and layup design is complex.
- Path planning: Appearance of lay-up defects due to non-geodetic curves. Defects like gaps and overlaps are intrinsic to complex parts.
- High raw material quality is needed (expensive material).
- Exact control of the tack is essential.
- ShapeProcess development: interaction of process parameters, material properties, and lay-up quality.
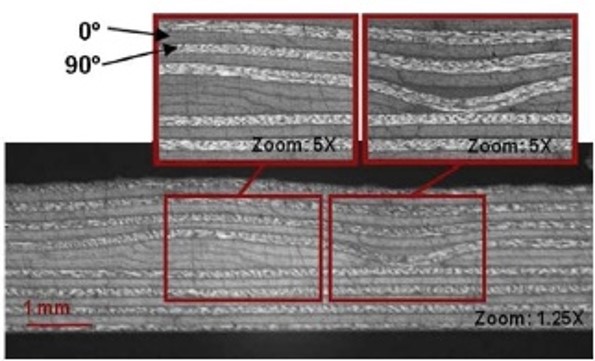
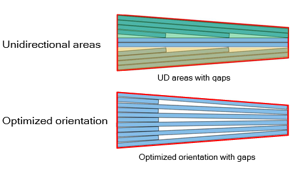
„Stepping Up the Game: Introducing AFP’s Formidable Manufacturing Adversary“
In composite manufacturing, each manufacturing technology is tailored for a specific purpose or sector. In the realm of wing covers, concepts are being explored to produce wings through Resin Transfer Molding (RTM), where the dry Fiber is positioned in the mold, the mold is closed, and resin is injected into it. AFP faces competition from RTM as the main contender in this case.
Sources
Croft et al 2011:
Kaven Croft, Larry Lessard, Damiano Pasini, Mehdi Hojjati, Jihua Chen, Ali Yousefpour,
Experimental study of the effect of automated fiber placement induced defects on performance of composite laminates,
Composites Part A: Applied Science and Manufacturing,
Volume 42, Issue 5,
2011,
Pages 484-491,
ISSN 1359-835X,
https://doi.org/10.1016/j.compositesa.2011.01.007.
0 Kommentare