A series of beyond 3D printing
“Meet Emre Osmanoglu, a Research Assistant at TUM’s Chair of Materials Engineering of Additive Manufacturing. In this interview, we dive into the realm of direct energy deposition technology, exploring the forefront of materials engineering. Gain unique insights into the latest advancements and challenges shaping the future of additive manufacturing.”
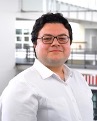
How would you explain the process to someone who has never heard of Direct Energy Deposition (DED)?
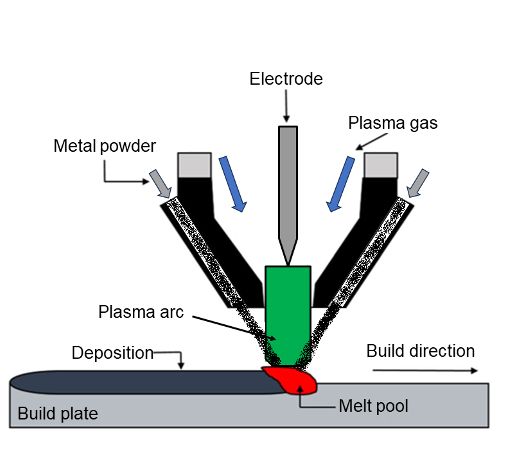
Diagram of a plasma arc welding process
Description automatically generatedText BoxText BoxIn DED, what we do is melt metal powders to create structures. The method of melting is distinctive for DED. I try to explain this process as if you have ever been to the seaside and built a sandcastle, while doing that you might have put some sand in your hand, wetted it, and just dropped wet sand out of your hand to build a wall-like structure. This is basically how DED works. We got these metal powders and sand, we make them liquid, add water, or in this case, add a lot of heat, melt the powders, and create a metal structure. DED is also a variation of the welding process, which might be much more understandable for someone with an engineering background. Picture (1) can explain it better. We have this heat source. We shoot powders to the heat source to melt the powders. This shooting creates a melt pool. As we move this heat source, the melt pool also moves, follows, and traces the heat source. As the heat source moves away, the melt pool cools down, solidifies, and creates this deposited structure on top of a metal plate. I described so far Powder-DED. There is also Wire-DED, which is also called wire arc additive manufacturing (WAAM). But my focus in our chair is on powder direct energy deposition. We use plasma gas as our heat source, but one can also use a laser beam or electron beam.
You mentioned WAAM and DED. Could you explain the basic difference between them?
The main difference is the material supply form. In Powder-DED, the metals are supplied in a powder form, and in wire arc additive manufacturing, the material is supplied in a wire form. It is easier to control the material flow in wire arc additive manufacturing because you are melting the wire. In powder-based methods, it is harder because you are shooting powder into the melt pool, and it might not melt.
What are some common materials used and which will be the economical method comparatively?
Theoretically, you can use any metal that you can melt with a laser or plasma. Plasma can practically melt any metal. Usually, steel alloys are used in DED. Nickel, copper, and aluminum alloys can also be used for these processes.
What are the benefits one would achieve utilizing DED?
The major advantage is free-form fabrication. You can build your structure in a very liberal way. But also, on top of it, you can combine materials which is either impossible or very hard to achieve with conventional methods. In casting, you cast a single material. In forging, you get a piece of metal, and you shape it. If you want to combine two different materials with conventional methods, you mainly use welding. You have one piece of metal; you have another type of metal, and you weld them together. In our case, you can combine different materials while building the structure. You can make in-situ alloying. That’s the focus of my research project. I’m investigating how to build functionally graded materials in which two types of material are combined to achieve a structure that has both properties of two metals. That is the major strength of the DED processes.
That sounds interesting! And what would you state as the disadvantages of DED?
The drawback would be the surface finishing. Post-processing is another step you need to do. In some cases, you are limited by your tool, i.e., for plasma arc, you cannot build intricate structures. To be more specific, in Plasma-DED, we cannot go below a thickness of 4 millimeters. It is not possible to construct a structure with small details directly; instead, it is necessary to build a larger structure and then use machining processes to make various structures. Of course, the flexibility of the process is a plus, but you might have to build support structures that have to be removed. It is common in most of the 3D printing processes and cannot defy the laws of physics. Depending on the material, another post-processing step might be heating treatment. For example, for aluminum, you need some heat treatment to age the aluminum.
Could you elaborate on your research objectives as you mentioned that your research involves the combination of two metals?
I work on the DISCO2030 project. This project is a part of the Horizon Europe 2030 projects. Our goal is to build structures with functionally graded materials. We are trying to combine the superior heat conductivity of copper with the structural integrity and strength of either steel or nickel alloys. So, in the project, there are three use cases. Figure (2) Among these three, we are focused on the rocket engine and heat exchanger. The burning chamber of the rocket engine will be manufactured out of copper and the exoskeleton will be out of nickel alloy. In the heat exchanger, the inside of the heat exchanger will be copper, or a copper alloy and the outside will be stainless steel. We are trying to combine these two materials. At TUM, our focus is this change region between these two materials The nickel alloy we use is Inconel 718. And copper alloy we use is CuCrZr. The stainless steel we use is 316L, but you can also use some other austenitic stainless steel like 304L – common materials.
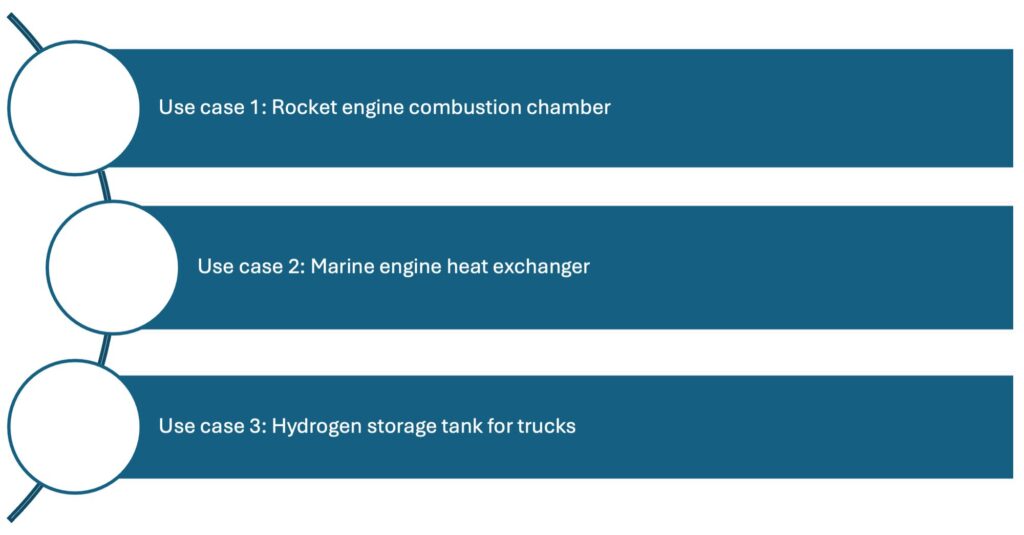
An exclusive info: Could you brief the experimental configuration employed in your research?
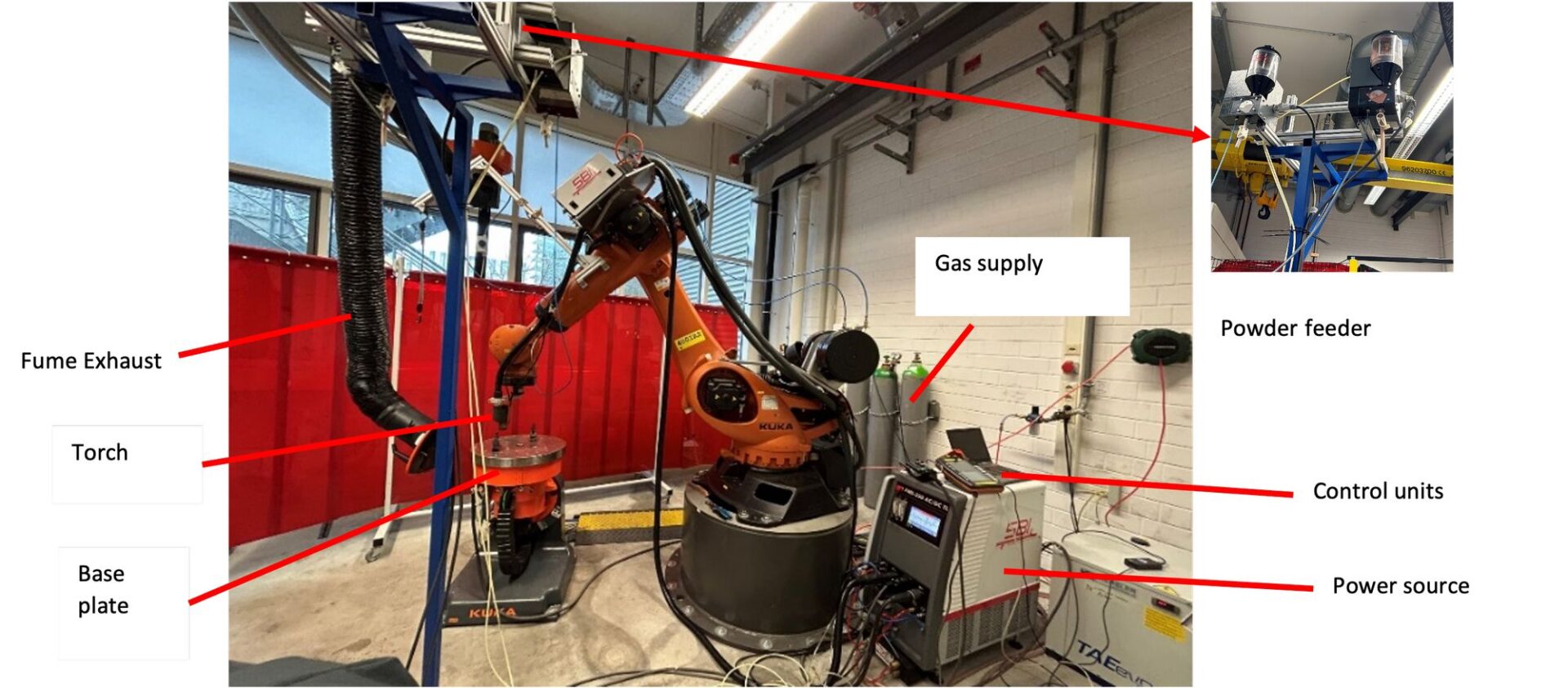
The experimental setup is a six-axis industrial robot arm. At the end of the robot arm, we attached a torch, which is a plasma welding device. Built into the torch, there is a powder feeding system. Currently, we have two different powder feeders attached to it – one for each material. And within the torch, within the powder sprayed area, the powders can mix. The powder is mixed in the weld pool. With this setup, we are building walls and cylindrical structures because those are the basic shapes to study the process, but you can technically use this setup to build any shape. We are using only plasma. We also use inert gases. You can use either argon or a mixture of argon-helium. If you add helium to the mixture, you can get a better result. You shouldn’t look directly at the plasma arc. It’s like looking directly at the sun. If you look directly at the sun, you get this bright spot when you close your eyes. This is the same happens with the torch. If you investigate it for longer with the naked eye, you might even go blind. That’s why we have these red covers. Other than that, you also must use a welder’s mask and filter mask because, during the process, we are not just melting the powders. We are technically vaporizing the powder itself. That’s also because of the different melting temperatures of different materials. For steel, the melting temperature is about 1,500 °C. For copper, it is 1,050 °C. So, this is about 400 °C difference. That’s why we also have a fume exhaust in here.
What are your comments about the surface finishing achieved from DED?
In DED, the surface finish depends both on the material and the power source. The surface finish is better using a laser beam. If you use plasma arc, the surface finish might be comparable to casting but maybe even worse. In these processes, you need post-processing to make sure that you provide the right output. The semi-finished object you obtain with this process, cannot be obtained with any other conventional method. You can build your object in a very fast manner with DED.
How do you handle the wastage of metal powders during manufacturing?
Plasma-DED we are making is not very environmentally friendly. Because our experimental setup is not a closed environment, the dedicated machines are closed. So, powder recycling is possible in this process because the powders splattered away are neither heated too much nor melted. You can recycle the powders. Research shows that recycled powders have almost no loss of mechanical properties except ductility. You can still get similar yield strengths and a structure with similar material properties. The problem is in our case, if you are also doing in-situ alloying, you must separate those two powders because you are also mixing two different materials. You are mixing copper with steel. If you can separate the residual powder, you can use it 100% again.
What is your biggest challenge in the project right now?
The main challenge here is that copper and iron do not have miscibility. They do not dissolve within each other. But we are trying to force them to create a mixed structure. It’s like oil and water. It is challenging because of the different behaviors of steel and copper. Copper has excellent thermal conductivity which is a problem in our case. We are trying to melt the copper, but the copper doesn’t want to melt as easily as steel because we are supplying heat with the plasma arc. The material doesn’t absorb the heat and if it absorbs the heat, it will just conduct the heat away very fast. When you are building on top of the copper structure, you supply heat at one point, but it just flows away within the structure which is not something we desire. We want to control the heat input and control the temperature field within the material, but it is challenging due to the thermal conductivity of copper. On the contrary, Printing steel is much easier, you also get better-looking structures when you are printing steel.
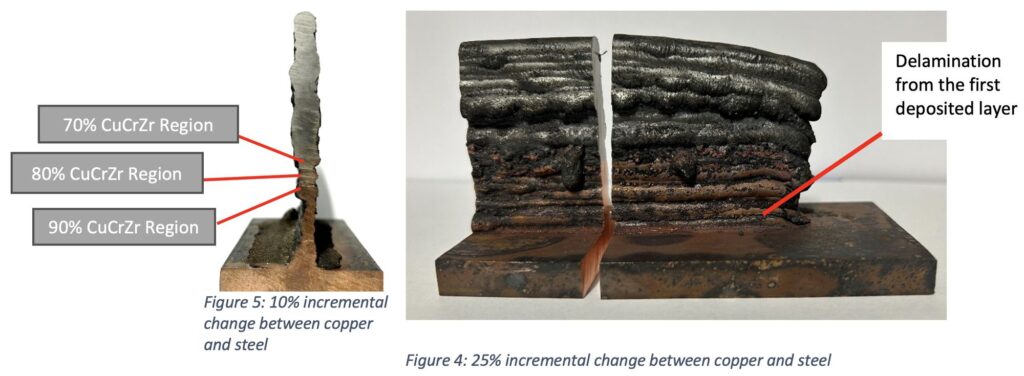
Wrapping up with: what are your thoughts about the future perspective of the DED?
Engineers try to use the best materials to build their designs but so far, we are limited with the methods we have—most of the time you must decide on one material and go with it. With DED, this limitation is removed and expands the whole industrial or mechanical engineering design to a new level. Previously, the structures had to be either made of a single material or you must weld two different metals together. With these new methods, you can generate a shape that is optimized for heat flow and can be a singular massive structure optimized for heat transfer made from two different metals – which is new for the manufacturing field. This will become the norm in machines that require high efficiency and high performance under extreme conditions: for metals, extremely corrosive environments, extreme temperatures, or large pressure differences like space. The future of DED will be integrated into basically any part that has to perform in these extreme conditions because a single material is not enough to perform under extreme conditions.
0 Kommentare